Five-axis redundant fiber-optic gyroscope measuring device structure
A fiber optic gyroscope and measuring device technology, applied in the field of inertial measurement, can solve the problems of single point failure, no redundant design of inertial instruments, poor heat dissipation of shock absorbers, etc., reduce reliability requirements and costs, and overcome heat transfer efficiency Effect of slow, good thermal design
- Summary
- Abstract
- Description
- Claims
- Application Information
AI Technical Summary
Problems solved by technology
Method used
Image
Examples
Embodiment Construction
[0031] The present invention will be further elaborated below in conjunction with embodiment.
[0032] The invention provides a five-axis redundant optical fiber gyro measuring device structure, which adopts five-way inertial instruments and five-way accelerometers to work independently and redundantly configure each other, rationally use the space, and has the advantages of small size, light weight, good heat dissipation, easy assembly Good workmanship and other advantages. The invention adopts a square box to carry a system circuit, a power supply, and three independent instruments to realize a multi-section layout in one box; the connection of each partition is connected by a relay electrical connector, which facilitates independent assembly of each partition and improves assembly efficiency ; The present invention adopts a ten-meter integrated structure design, which is convenient for centralized vibration reduction and heat insulation of high-precision instruments; ration...
PUM
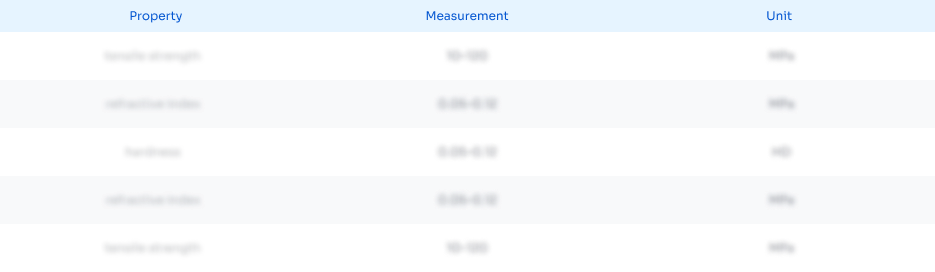
Abstract
Description
Claims
Application Information

- R&D Engineer
- R&D Manager
- IP Professional
- Industry Leading Data Capabilities
- Powerful AI technology
- Patent DNA Extraction
Browse by: Latest US Patents, China's latest patents, Technical Efficacy Thesaurus, Application Domain, Technology Topic, Popular Technical Reports.
© 2024 PatSnap. All rights reserved.Legal|Privacy policy|Modern Slavery Act Transparency Statement|Sitemap|About US| Contact US: help@patsnap.com