Structure for preventing lubricating oil coking and leakage deflagration at inter-turbine casings
A technology for handling lubricating oil and turbine, which is applied in the structural field of preventing lubricating oil coking and leakage and deflagration at the casing between turbines
- Summary
- Abstract
- Description
- Claims
- Application Information
AI Technical Summary
Problems solved by technology
Method used
Image
Examples
Embodiment Construction
[0047] In order to make the purpose, technical solution and advantages of the application more clear, the technical solution in the embodiment of the application will be described in more detail below in conjunction with the drawings in the embodiment of the application.
[0048] Such as Figure 1 to Figure 3 As shown, the structure provided by the present application to prevent lubricating oil coking and leaking deflagration at the casing between turbines is mainly realized by using a double-layer isolated combined pipe joint 6, and the structure mainly includes:
[0049] The high-pressure turbine 1 and the low-pressure turbine 2, between the high-pressure turbine 1 and the low-pressure turbine 2, flow the ultra-high temperature main channel gas Q4;
[0050] Between the high-pressure turbine 1 and the low-pressure turbine 2, an inter-turbine casing is arranged, that is, the outer casing 4 between the turbines and the inner casing 5 between the turbines, and the rectifying gui...
PUM
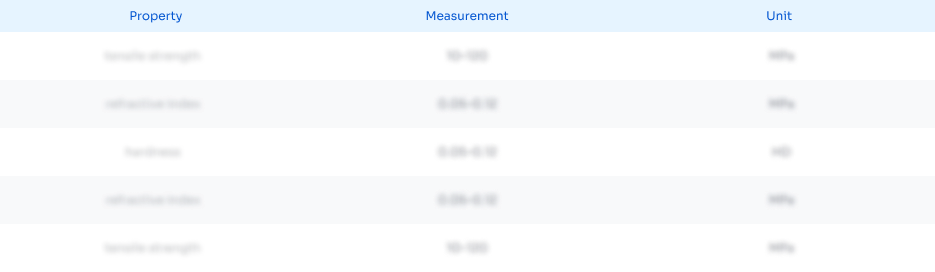
Abstract
Description
Claims
Application Information

- R&D
- Intellectual Property
- Life Sciences
- Materials
- Tech Scout
- Unparalleled Data Quality
- Higher Quality Content
- 60% Fewer Hallucinations
Browse by: Latest US Patents, China's latest patents, Technical Efficacy Thesaurus, Application Domain, Technology Topic, Popular Technical Reports.
© 2025 PatSnap. All rights reserved.Legal|Privacy policy|Modern Slavery Act Transparency Statement|Sitemap|About US| Contact US: help@patsnap.com