Multi-step multi-contour coating forming reaming and milling cutter
A multi-contour, multi-step technology, applied in the field of processing tools, can solve the problems of poor coaxiality, high processing cost, and milling cutter breakage, etc., to save processing time and tool setting time, and enhance support and firmness, and the effect of improving the accuracy of shape and position tolerances
- Summary
- Abstract
- Description
- Claims
- Application Information
AI Technical Summary
Problems solved by technology
Method used
Image
Examples
Embodiment Construction
[0025] The specific implementation manners of the present invention will be further described in detail below in conjunction with the accompanying drawings and embodiments. The following examples are used to illustrate the present invention, but are not intended to limit the scope of the present invention.
[0026] In describing the present invention, it is to be understood that the terms "upper", "lower", "left", "right", "front", "rear", "top", "bottom" etc. indicate an orientation or position The relationship is based on the orientation or positional relationship shown in the drawings, and is only for the convenience of describing the present invention and simplifying the description, rather than indicating or implying that the machine or element referred to must have a specific orientation, be constructed and operated in a specific orientation, therefore It should not be construed as a limitation of the present invention. It should be understood that the terms "first", "s...
PUM
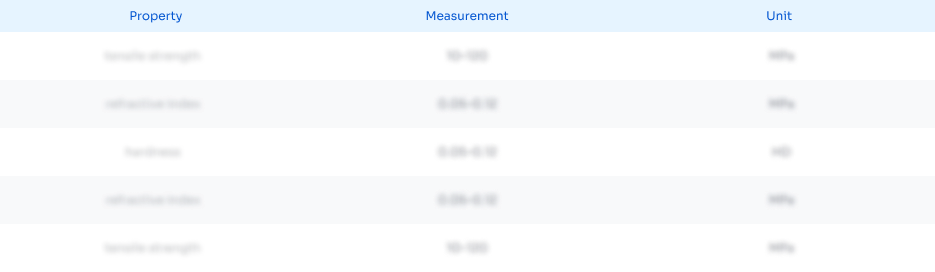
Abstract
Description
Claims
Application Information

- R&D Engineer
- R&D Manager
- IP Professional
- Industry Leading Data Capabilities
- Powerful AI technology
- Patent DNA Extraction
Browse by: Latest US Patents, China's latest patents, Technical Efficacy Thesaurus, Application Domain, Technology Topic, Popular Technical Reports.
© 2024 PatSnap. All rights reserved.Legal|Privacy policy|Modern Slavery Act Transparency Statement|Sitemap|About US| Contact US: help@patsnap.com