RPE/UHMWPEF composite material and preparation method and application thereof
A composite material and raw material technology, applied in the field of recycling of waste polymer materials, can solve the problems of thermomechanical degradation, poor mechanical stability, balanced rigidity and toughness of composite materials, etc. Effect
- Summary
- Abstract
- Description
- Claims
- Application Information
AI Technical Summary
Problems solved by technology
Method used
Image
Examples
Embodiment 1
[0036] This example provides 6 kinds of rPE / UHMWPEF composite materials and their preparation methods, and provides pure rPE as a basic control group.
[0037] According to the formula of sample numbers 1-6 shown in Table 1, the ingredients were mixed, pre-mixed in a high-speed mixer for 10 minutes, and then melted and co-mixed using an eccentric rotor extruder, a plasticizing and transporting equipment for polymer materials based on elongational rheology. Mixing, the temperature of each stage is 180-190-200-210 ℃, the rotor speed is 80 rpm, extrusion molding, qualitative by three rolls, cooling, and drying to obtain 6 kinds of rPE / UHMWPEF composite materials.
[0038] The above composite material was dried in a vacuum drying oven at 70°C for 8 hours, and the tensile performance test was carried out according to GB / T 1040-2006. The results are shown in Table 3. Among them, it can be seen from Table 3 that when the mass ratio of rPE, chopped UHMWPEF, calcium carbonate, POE-g-MA...
Embodiment 2
[0042] This example provides 6 kinds of rPE / UHMWPEF composite materials and their preparation methods, which are used as corresponding comparative examples in Example 1.
[0043] According to the formula of sample numbers 7 to 12 shown in Table 2, the ingredients were mixed, pre-mixed in a high-speed mixer for 10 minutes, and then melt-blended using a traditional twin-screw extruder based on shear rheology, and the temperature of each section was 180 -185-190-195-200-210-210°C, the rotor speed is 80 r / min, extruded, qualified by three rolls, cooled and dried to obtain 6 kinds of rPE / UHMWPEF composite materials.
[0044] The above composite material was dried in a vacuum oven at 70°C for 8 hours, and the tensile properties were tested according to GB / T 1040-2006. The results are shown in Table 4. Among them, comparing Table 3 and Table 4, it can be seen that the tensile strength and elongation at break of all composite materials are lower than the components of the same proport...
PUM
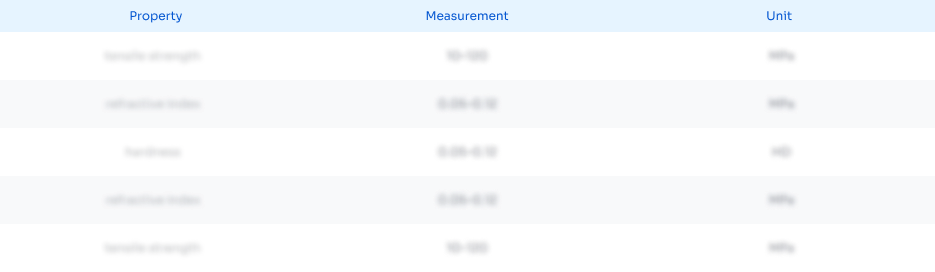
Abstract
Description
Claims
Application Information

- Generate Ideas
- Intellectual Property
- Life Sciences
- Materials
- Tech Scout
- Unparalleled Data Quality
- Higher Quality Content
- 60% Fewer Hallucinations
Browse by: Latest US Patents, China's latest patents, Technical Efficacy Thesaurus, Application Domain, Technology Topic, Popular Technical Reports.
© 2025 PatSnap. All rights reserved.Legal|Privacy policy|Modern Slavery Act Transparency Statement|Sitemap|About US| Contact US: help@patsnap.com