Method for preparing 5-hydroxymethylfurfural through conversion of cellulose in composite molten salt hydrate
A technology of hydroxymethyl furfural and composite molten salt, which is applied in the field of biomass resource utilization, can solve the problems of insoluble cellulose, low yield of 5-hydroxymethyl furfural and the like, achieves simple preparation, low price, and prevents side effects. The effect of product formation
- Summary
- Abstract
- Description
- Claims
- Application Information
AI Technical Summary
Problems solved by technology
Method used
Image
Examples
example 1
[0029] (1) ZnCl 2 ·3H 2 O and FeCl 3 ·6H 2 O two kinds of molten salt hydrates are mixed according to a volume ratio of 3:1 to obtain a composite molten salt hydrate;
[0030] (2) Mix 5ml of composite molten salt hydrate with 0.2g of cellulose, then add 15ml of methyl isobutyl ketone to the composite molten salt hydrate to obtain a two-phase system mixture;
[0031] (3) Put the two-phase mixed solution obtained in step (2) into a hydrothermal kettle, and when the temperature in the oil bath reaches 110° C., put it into the hydrothermal kettle and start stirring, carry out a catalytic reaction for 120 minutes, and after the reaction finishes, take The organic phase is separated and purified to obtain 5-hydroxymethylfurfural.
[0032] According to high performance liquid chromatography analysis, 5-hydroxymethylfurfural was obtained in a yield of 47.6%.
example 2
[0034] (1) ZnCl 2 ·3H 2 O and CuCl 2 2H 2 O two kinds of molten salt hydrates are mixed according to a volume ratio of 2:1 to obtain a composite molten salt hydrate;
[0035] (2) Take 5ml of composite molten salt hydrate and mix it with 0.15g of cellulose, then add 5ml of petroleum ether to the composite molten salt hydrate to obtain a two-phase system mixed solution;
[0036] (3) Put the two-phase mixed solution obtained in step (2) into a hydrothermal kettle, and when the temperature in the oil bath reaches 120° C., put it into the hydrothermal kettle and start stirring, and carry out a catalytic reaction for 30 minutes. After the reaction, take The organic phase is separated and purified to obtain 5-hydroxymethylfurfural.
[0037] According to HPLC analysis, 5-hydroxymethylfurfural was obtained in a yield of 20.5%.
example 3
[0039] (1) FeCl 3 ·6H 2 O and CuCl 2 2H 2 O two kinds of molten salt hydrates are mixed according to a volume ratio of 1.5:1 to obtain a composite molten salt hydrate;
[0040] (2) Take 5ml of composite molten salt hydrate and mix it with 0.1g of cellulose, then add 10ml of hexane to the composite molten salt hydrate to obtain a two-phase system mixed solution;
[0041] (3) Put the two-phase mixed solution obtained in step (2) into the hydrothermal kettle, and when the temperature in the oil bath reaches 125° C., put it into the hydrothermal kettle and start stirring, carry out the catalytic reaction for 45 minutes, and after the reaction finishes, take The organic phase is separated and purified to obtain 5-hydroxymethylfurfural.
[0042] According to high-performance liquid chromatography analysis, 5-hydroxymethylfurfural was obtained in a yield of 27.8%.
PUM
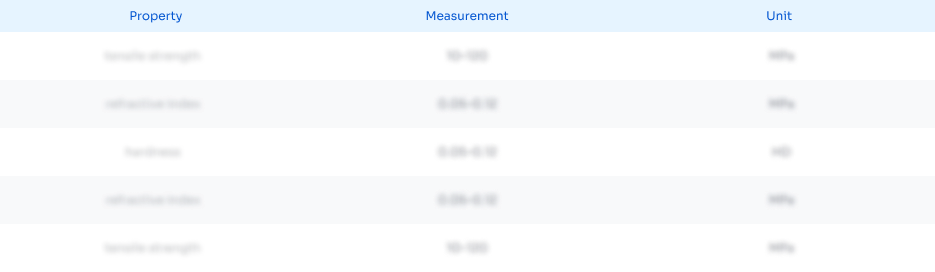
Abstract
Description
Claims
Application Information

- R&D Engineer
- R&D Manager
- IP Professional
- Industry Leading Data Capabilities
- Powerful AI technology
- Patent DNA Extraction
Browse by: Latest US Patents, China's latest patents, Technical Efficacy Thesaurus, Application Domain, Technology Topic, Popular Technical Reports.
© 2024 PatSnap. All rights reserved.Legal|Privacy policy|Modern Slavery Act Transparency Statement|Sitemap|About US| Contact US: help@patsnap.com