Nb, V and Ti microalloyed gear steel and preparation method thereof, heat treatment method and carburizing treatment method thereof and carburized gear steel
A heat treatment method and micro-alloying technology, applied in metal material coating process, coating, solid-state diffusion coating, etc., can solve the problems of materials that cannot adapt to high contact fatigue performance
- Summary
- Abstract
- Description
- Claims
- Application Information
AI Technical Summary
Problems solved by technology
Method used
Image
Examples
Embodiment Construction
[0075] A kind of Nb, V, Ti micro-alloyed gear steel, comprising the following chemical components in weight percentage: C: 0.15-0.19%, Si: 0.15-0.30%, Mn: 0.60-0.90%, Cr: 1.60-1.80%, Mo : 0.20~0.35%, Nb: 0.025~0.040%, Ni: 1.50~1.70%, Al: 0.020~0.040%, P: ≤0.010%, S: ≤0.010%, V: 0.05~0.15%, Ti 0.05~0.15 %, T.O: ≤10ppm, [H]: ≤1.0ppm, [N]: ≤80ppm, the rest are Fe and unavoidable impurity elements, among them, Km=C+Mn / 6+(Cr+Mo+V) / 5+(Ni+Cu) / 15+10Nb+Al / 15(N-Ti / 3.4), and Km: 0.97-1.37.
[0076] It adopts the process of electric arc furnace smelting-LF refining-RH vacuum treatment-continuous casting-hot rolling-slow cooling, as follows:
[0077] It adopts the process of electric arc furnace smelting-LF refining-RH vacuum treatment-continuous casting-hot rolling-slow cooling, as follows:
[0078] The continuous casting slab is heated and kept at 1230-1280°C for ≥5 hours before round steel rolling. The rolling start temperature is 1120-1180°C and the final rolling temperature is 930-...
PUM
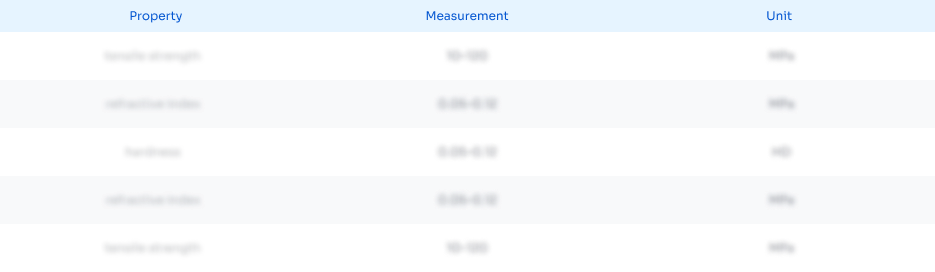
Abstract
Description
Claims
Application Information

- Generate Ideas
- Intellectual Property
- Life Sciences
- Materials
- Tech Scout
- Unparalleled Data Quality
- Higher Quality Content
- 60% Fewer Hallucinations
Browse by: Latest US Patents, China's latest patents, Technical Efficacy Thesaurus, Application Domain, Technology Topic, Popular Technical Reports.
© 2025 PatSnap. All rights reserved.Legal|Privacy policy|Modern Slavery Act Transparency Statement|Sitemap|About US| Contact US: help@patsnap.com