Threaded pipe production process
A production process and threaded pipe technology, applied in the field of threaded pipe production technology, can solve the problems of reducing the service life of spinning rings and inner cores, affecting the quality of spinning forming, etc.
- Summary
- Abstract
- Description
- Claims
- Application Information
AI Technical Summary
Problems solved by technology
Method used
Image
Examples
Embodiment
[0038] The embodiment is basically as attached Figure 1 to Figure 3 Shown:
[0039] The threaded pipe production process requires the use of threaded pipe production equipment, an inner core for spinning and a traction device for pulling the pipe. The traction device is used to pull the pipe forward. The inner core includes a core rod, a threaded core and a floating core. Both the threaded core head and the floating core head are fixedly connected to the core rod; the threaded pipe production equipment includes a shell 1, a driver 2 and a spinning ring 3, the drive 2 adopts an electric spindle, the drive 2 is fixedly connected to the shell 1, and the drive 2 is used to drive the spinning ring 3 to rotate, the spinning ring 3 has a steel ball 31, and the casing 1 is horizontally slidably connected with a moving plug 4 (to fix the moving plug 4, a locking screw 11 is installed on the casing 1 , the locking screw 11 can be tightly pressed against the moving plug 4), the moving ...
PUM
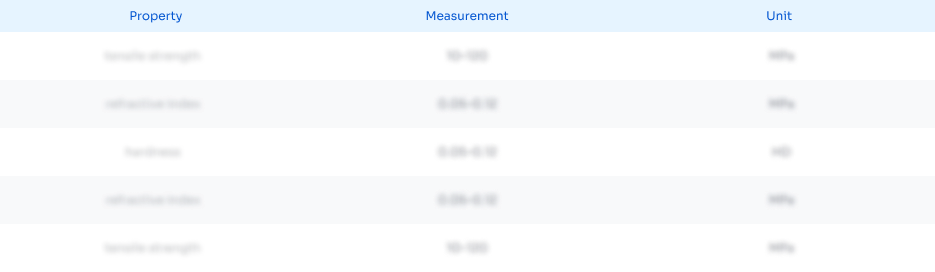
Abstract
Description
Claims
Application Information

- Generate Ideas
- Intellectual Property
- Life Sciences
- Materials
- Tech Scout
- Unparalleled Data Quality
- Higher Quality Content
- 60% Fewer Hallucinations
Browse by: Latest US Patents, China's latest patents, Technical Efficacy Thesaurus, Application Domain, Technology Topic, Popular Technical Reports.
© 2025 PatSnap. All rights reserved.Legal|Privacy policy|Modern Slavery Act Transparency Statement|Sitemap|About US| Contact US: help@patsnap.com