Cleaning method used before coating of hard alloy numerical control blade
A cemented carbide, pre-coating technology, applied in the field of carbide CNC coated blade production
- Summary
- Abstract
- Description
- Claims
- Application Information
AI Technical Summary
Problems solved by technology
Method used
Image
Examples
Embodiment 1
[0053] Embodiment 1: Cleaning before coating of cemented carbide CNC inserts
[0054] The specific operation steps are as follows:
[0055] S1. Add No. 1 cleaning solution (strong alkaline metal cleaning solution) to No. 1 cleaning tank of the ultrasonic cleaner, set the heating temperature of the tank to 60°C, and set the ultrasonic rinsing time to 6.5 minutes;
[0056] Preparation of No. 1 cleaning solution: Mix 5L of A solution, 5L of B solution and 90L of deionized pure water to obtain 100L of No. 1 cleaning solution; wherein: A solution contains 22% potassium hydroxide in terms of mass percentage , polyethylene glycol 3%, dimethyl betaine 3%, polyhydroxy acid 3%, and the balance is pure water; B solution contains aminoethanol 22%, polyoxyethylene fatty amine 10%, fat amide 10%, ammonium chloride 10%, coconut acid diethanolamide 3%, ethylene glycol 3%, and the balance is pure water.
[0057] S2. Add No. 2 cleaning solution into the No. 2 cleaning tank of the ultrasonic c...
Embodiment 2
[0068] Embodiment 2: Cleaning before coating of cemented carbide CNC inserts
[0069] The specific operation steps are as follows:
[0070] S1. Add No. 1 cleaning solution (strong alkaline metal cleaning solution) into the No. 1 cleaning tank of the ultrasonic cleaning machine, and set the heating temperature of the tank to 50°C, and set the ultrasonic rinsing time to 7 minutes;
[0071] Preparation of No. 1 cleaning solution: Mix 6L of A solution, 6L of B solution and 88L of deionized pure water to obtain 100L of No. 1 cleaning solution; wherein: A solution contains 30% potassium hydroxide in terms of mass percentage , polyethylene glycol 5%, dimethyl betaine 5%, polyhydroxy acid 5%, and the balance is pure water; B solution contains aminoethanol 30%, polyoxyethylene fatty amine 15%, fat amide 15%, ammonium chloride 15%, coconut acid diethanolamide 5%, ethylene glycol 5%, and the balance is pure water.
[0072] S2. Add No. 2 cleaning solution into the No. 2 cleaning tank of...
Embodiment 3
[0083] Embodiment 3: Cleaning before coating of cemented carbide numerically controlled inserts
[0084] The specific operation steps are as follows:
[0085] S1. Add No. 1 cleaning solution (strong alkaline metal cleaning solution) into the No. 1 cleaning tank of the ultrasonic cleaning machine, and set the heating temperature of the tank to 65°C, and set the ultrasonic rinsing time to 6 minutes;
[0086] Preparation of No. 1 cleaning solution: Mix 4L of A solution, 4L of B solution and 92L of deionized pure water to obtain 100L of No. 1 cleaning solution; wherein: A solution contains 15% potassium hydroxide in terms of mass percentage , polyethylene glycol 1%, dimethyl betaine 1%, polyhydroxy acid 1%, and the balance is pure water; B solution contains aminoethanol 15%, polyoxyethylene fatty amine 5%, fat amide 5%, ammonium chloride 5%, coconut acid diethanolamide 1%, ethylene glycol 1%, and the balance is pure water.
[0087] S2. Add No. 2 cleaning solution into the No. 2 ...
PUM
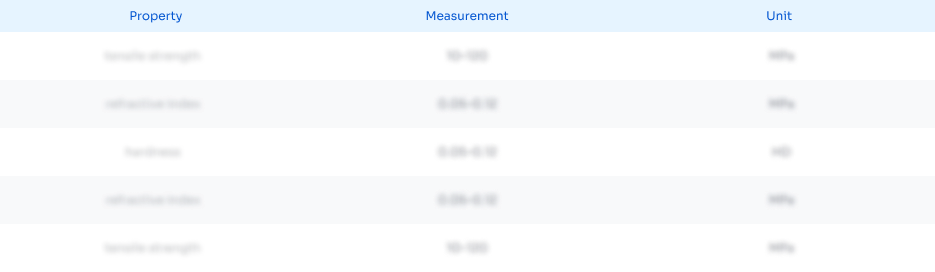
Abstract
Description
Claims
Application Information

- R&D
- Intellectual Property
- Life Sciences
- Materials
- Tech Scout
- Unparalleled Data Quality
- Higher Quality Content
- 60% Fewer Hallucinations
Browse by: Latest US Patents, China's latest patents, Technical Efficacy Thesaurus, Application Domain, Technology Topic, Popular Technical Reports.
© 2025 PatSnap. All rights reserved.Legal|Privacy policy|Modern Slavery Act Transparency Statement|Sitemap|About US| Contact US: help@patsnap.com