Pipe diameter self-adaptive pipeline detection robot
A pipeline inspection and robot technology, applied in the direction of pipes/pipe joints/fittings, instruments, pipe components, etc., can solve the problem of low detection accuracy, difficult detection of industrial pipelines, and inability to accurately detect small-scale geometric defects and damages on the inner wall of the pipeline. problem, to achieve the effect of large load and reliability, strong ability to adapt to the ground environment, and improve detection ability
- Summary
- Abstract
- Description
- Claims
- Application Information
AI Technical Summary
Problems solved by technology
Method used
Image
Examples
Embodiment Construction
[0025] The technical solution of the present invention will be clearly and completely described below in conjunction with the accompanying drawings. It should be noted that the illustrations provided in this embodiment are only schematically illustrating the basic concept of the present invention. , "Up", "Down", "Front", "Back", "Left", "Right", "Vertical", "Horizontal", "Top", "Bottom", "Inner", "Outer", etc. The indicated orientation or positional relationship is based on the orientation or positional relationship shown in the drawings, and is only for the convenience of describing the present invention and simplifying the description, rather than indicating or implying that the referred device or element must have a specific orientation, or in a specific orientation. construction and operation, therefore, should not be construed as limiting the invention.
[0026] The present invention aims at the defects that the existing pipeline detection robot has low detection accurac...
PUM
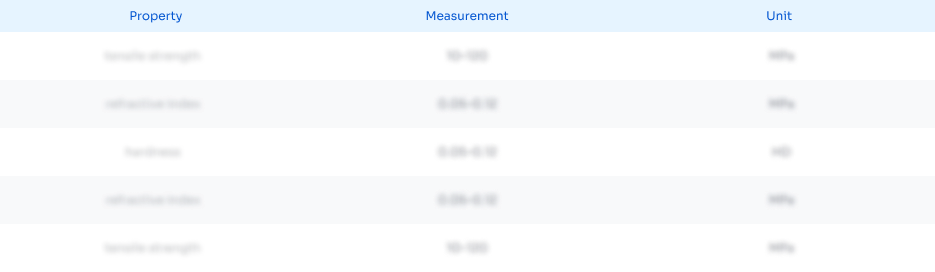
Abstract
Description
Claims
Application Information

- R&D
- Intellectual Property
- Life Sciences
- Materials
- Tech Scout
- Unparalleled Data Quality
- Higher Quality Content
- 60% Fewer Hallucinations
Browse by: Latest US Patents, China's latest patents, Technical Efficacy Thesaurus, Application Domain, Technology Topic, Popular Technical Reports.
© 2025 PatSnap. All rights reserved.Legal|Privacy policy|Modern Slavery Act Transparency Statement|Sitemap|About US| Contact US: help@patsnap.com