A multi-objective optimization design method for inner diameter structure of hollow stepped shaft
A technology of multi-objective optimization and design method, which is applied in the field of multi-objective optimization design of the inner diameter structure of hollow stepped shafts, can solve the problems of single optimization target, repeated checking, and few design variables, so as to achieve fast convergence speed, improve design efficiency, The effect of improving material utilization
- Summary
- Abstract
- Description
- Claims
- Application Information
AI Technical Summary
Problems solved by technology
Method used
Image
Examples
Embodiment Construction
[0058] The following will clearly and completely describe the technical solutions in the embodiments of the present invention in conjunction with the embodiments of the present invention. Obviously, the described embodiments are only part of the embodiments of the present invention, not all of them. Based on the implementation manners in the present invention, all other implementation manners obtained by persons of ordinary skill in the art without making creative efforts belong to the scope of protection of the present invention.
[0059] Such as figure 1 As shown, the embodiment of the present invention discloses a multi-objective optimization design method for the inner diameter structure of a hollow stepped shaft, including the following steps:
[0060] Step 1. According to the actual boundary conditions of the hollow stepped shaft in the motor rotor, a finite element model of the hollow stepped shaft is established;
[0061] In this application, as an example, the number...
PUM
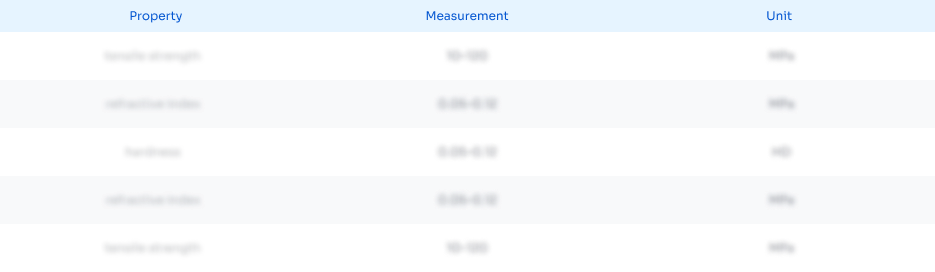
Abstract
Description
Claims
Application Information

- R&D Engineer
- R&D Manager
- IP Professional
- Industry Leading Data Capabilities
- Powerful AI technology
- Patent DNA Extraction
Browse by: Latest US Patents, China's latest patents, Technical Efficacy Thesaurus, Application Domain, Technology Topic, Popular Technical Reports.
© 2024 PatSnap. All rights reserved.Legal|Privacy policy|Modern Slavery Act Transparency Statement|Sitemap|About US| Contact US: help@patsnap.com