A Target Decomposition Method for Chassis Components Based on Robust Optimization
A technology of objective decomposition and robust optimization, applied in multi-objective optimization, design optimization/simulation, geometric CAD, etc., to reduce the optimization dimension and optimization difficulty, reduce simulation solution time, and realize the effect of automation
- Summary
- Abstract
- Description
- Claims
- Application Information
AI Technical Summary
Problems solved by technology
Method used
Image
Examples
Embodiment Construction
[0041]
[0042]
[0043]
[0044] The DOE design matrix was built using the Latin hypercube method, given 801 sample points. Call the parameters created in step 1.3
[0046]
[0050]
[0051]
[0053] The key hard point position deviation distribution function is set to be a normal distribution function, and its standard deviation is 0.1 mm. Based on step 3
[0055]
[0056]
[0057] Call the rear suspension K characteristic analysis model to verify the optimization results, and the verification results are shown in Table 5. Results from Table 5
[0059]
[0060]
[0064]
[0065]
[0066] The DOE design matrix was built using the Latin hypercube method, given 500 sample points. Call the parameters created in step 1.3
[0068]
[0072]
[0076]
[0077]
[0078] Call the rear suspension C characteristic analysis model to verify the optimization results, and the verification results are shown in Table 10. From Table 10 can be
[0080]
[0081]
PUM
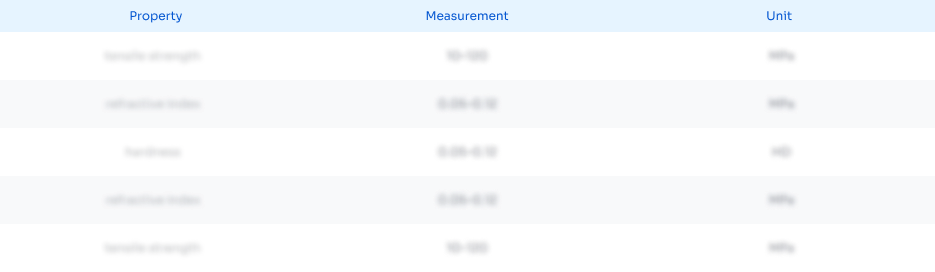
Abstract
Description
Claims
Application Information

- Generate Ideas
- Intellectual Property
- Life Sciences
- Materials
- Tech Scout
- Unparalleled Data Quality
- Higher Quality Content
- 60% Fewer Hallucinations
Browse by: Latest US Patents, China's latest patents, Technical Efficacy Thesaurus, Application Domain, Technology Topic, Popular Technical Reports.
© 2025 PatSnap. All rights reserved.Legal|Privacy policy|Modern Slavery Act Transparency Statement|Sitemap|About US| Contact US: help@patsnap.com