Chip-level disc type acousto-optic standing wave gyroscope
A disc-type, chip-level technology, applied in the field of micro-sensors, can solve the problems of attenuation signal sensitivity, small secondary surface acoustic wave area, and scattered distribution of waveguides in key components, so as to improve signal conversion rate, avoid bending loss, improve The effect of sensitivity
- Summary
- Abstract
- Description
- Claims
- Application Information
AI Technical Summary
Problems solved by technology
Method used
Image
Examples
specific Embodiment
[0041] The substrate material used in the chip-level disc-type acousto-optic standing wave gyroscope in this embodiment is lithium niobate crystal-insulator (LNOI), that is, from top to bottom, it is lithium niobate thin film layer-silicon dioxide crystal layer- Lithium niobate crystal layer, the gyro structure placed on the upper surface of the substrate includes two parts: an acoustic wave drive module and an optical detection module, wherein the acoustic wave drive module is formed by sputtering metal on the surface of the uppermost film layer of the LNOI substrate, and the optical detection module is formed by It is achieved by etching the uppermost thin film layer on the LNOI substrate.
[0042] The thickness of the uppermost film layer of the LNOI substrate is 500nm; in the acoustic wave driving module, the first fork 1-1, the second fork 1-2, the third fork 1-3 and the fourth fork 1-4 are formed The inner radius, outer radius and thickness of the ring-shaped interdigita...
PUM
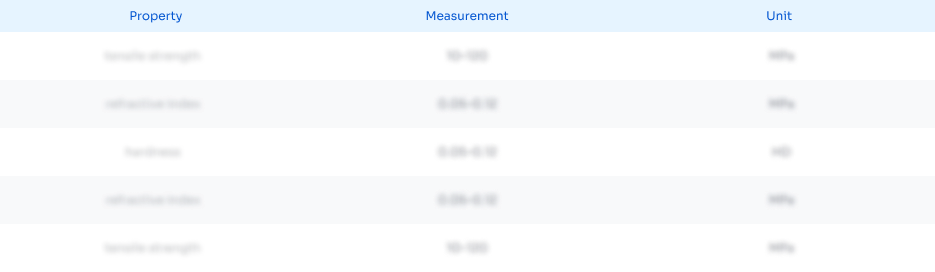
Abstract
Description
Claims
Application Information

- R&D Engineer
- R&D Manager
- IP Professional
- Industry Leading Data Capabilities
- Powerful AI technology
- Patent DNA Extraction
Browse by: Latest US Patents, China's latest patents, Technical Efficacy Thesaurus, Application Domain, Technology Topic, Popular Technical Reports.
© 2024 PatSnap. All rights reserved.Legal|Privacy policy|Modern Slavery Act Transparency Statement|Sitemap|About US| Contact US: help@patsnap.com