Carburizing heat treatment process for fatigue-resistant metal sliding block
A technology of fatigue resistance and sliding block, applied in the field of heat treatment, can solve the problem of reducing the ability of inward diffusion, and achieve the effect of smoothing the hardness gradient and improving the contact fatigue performance.
- Summary
- Abstract
- Description
- Claims
- Application Information
AI Technical Summary
Problems solved by technology
Method used
Image
Examples
Embodiment Construction
[0024] see figure 1 , CP in the figure refers to the carbon potential in the furnace.
[0025] The carburizing heat treatment process of the fatigue-resistant metal slider includes the following steps:
[0026] S1. Put the slider into the preheating furnace to preheat to 350°C, and the preheating time is 1h;
[0027] S2. Put the slider into a box-type controlled atmosphere carburizing furnace for carburizing and quenching; specifically include
[0028] S21, soaking to 880°C, soaking time is 0.5h, CP is 0.4;
[0029] S22. Heating to 935°C for the first intensive infiltration for 2.5 hours and a CP of 1.3; for the first diffusion for 2 hours and a CP of 1.1; then for the second intensive infiltration for 4 hours and a CP of 1.3 It is 1.2; then carry out the second diffusion, the time is 2.5h, and the CP is 1.0; prevent one-stage high carbon potential and strong infiltration from causing surface carbon accumulation and cementite; the design of decreasing carbon potential makes...
PUM
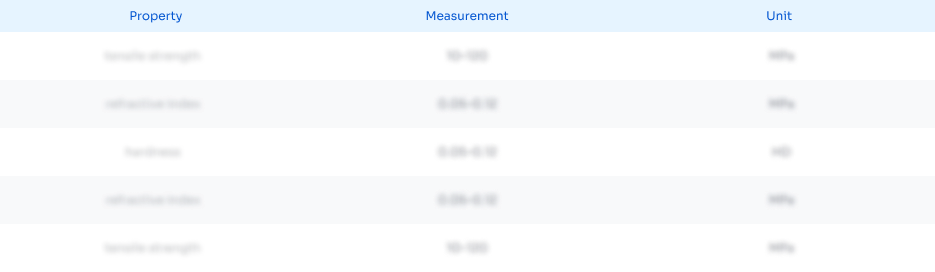
Abstract
Description
Claims
Application Information

- R&D Engineer
- R&D Manager
- IP Professional
- Industry Leading Data Capabilities
- Powerful AI technology
- Patent DNA Extraction
Browse by: Latest US Patents, China's latest patents, Technical Efficacy Thesaurus, Application Domain, Technology Topic, Popular Technical Reports.
© 2024 PatSnap. All rights reserved.Legal|Privacy policy|Modern Slavery Act Transparency Statement|Sitemap|About US| Contact US: help@patsnap.com