Beneficiation method for recovering uranium from rare earth ore
A beneficiation method and a technology for recovering uranium, which are applied in the field of uranium resource beneficiation, can solve the problems of low uranium content, difficult separation and enrichment of uranium, complex uranium occurrence state, etc., and achieve the effects of reducing radioactive hazards and high-efficiency enrichment.
- Summary
- Abstract
- Description
- Claims
- Application Information
AI Technical Summary
Problems solved by technology
Method used
Image
Examples
Embodiment 1
[0064] A rare earth mine in northern my country mainly includes bastnaesite, xing'anite, brown yttrium niobium ore, pyrochlore, thorite, fractalite, magnetite, quartz, zircon, feldspar, chlorite, calcite, black Mica and other mineral composition, REO content 0.92%, U content 0.021%.
[0065] In this example, the flotation effects of uranium minerals added with uranium mineral activator lead nitrate and without uranium mineral activator were compared, and the test numbers were test A and test B respectively.
[0066] (1) The ores in test A and test B were crushed to -12mm respectively, and then the fine-grained ores below -0.5mm were separated with a sieve to obtain +0.5mm coarse-grained ore and -0.5mm fine-grained ore.
[0067] (2) Adjust the density of the dense medium suspension to 1.5kg / m 3 , the dense medium feed pressure is set to 110kPa, the ratio of the ore volume fed to the resuspension liquid volume is 1:5, and the +0.5mm coarse-grained grade of test A and test B are ...
Embodiment 2
[0082]A rare earth mine in northern my country mainly includes bastnaesite, xing'anite, brown yttrium niobium ore, pyrochlore, thorite, fractalite, magnetite, quartz, zircon, feldspar, chlorite, calcite, black Mica and other mineral composition, REO content 0.92%, U content 0.021%.
[0083] (1) Crush the ore to -10mm, and then use a sieve to separate the fine-grained ore below -1mm to obtain +1mm coarse-grained ore and -1mm fine-grained ore.
[0084] (2) Adjust the density of the dense medium suspension to 1.8kg / m 3 , the feeding pressure of the dense medium is set to 120kPa, the ratio of the solid volume of the ore fed to the volume of the resuspension liquid is 1:4.5, and the +1mm coarse-grained ore is separated by a dense medium cyclone to obtain a gravity concentration concentrate And re-election tailings I.
[0085] (3) Under the condition of magnetic field intensity 17000Oe, classify-1mm fine-grained ore with strong magnetic separator, obtain magnetic separation concent...
Embodiment 3
[0098] A rare earth mine in northern my country mainly includes bastnaesite, xing'anite, brown yttrium niobium ore, pyrochlore, thorite, fractalite, magnetite, quartz, zircon, feldspar, chlorite, calcite, black Mica and other mineral composition, REO content 0.92%, U content 0.021%.
[0099] In this example, the flotation effects of uranium minerals added with trialkyl oxyphosphorus as an auxiliary collector for uranium minerals and those without auxiliary collectors for uranium minerals were compared, and the test numbers were test A and test B respectively.
[0100] (1) The ores in test A and test B were crushed to -10mm respectively, and then the fine-grained ores below -1mm were separated with a sieve to obtain +1mm coarse-grained ore and -1mm fine-grained ore.
[0101] (2) Adjust the density of the dense medium suspension to 2.0kg / m 3 , the dense medium feed pressure is set to 140kPa, the ratio of the volume of the ore fed to the volume of the resuspension is 1:4, and the...
PUM
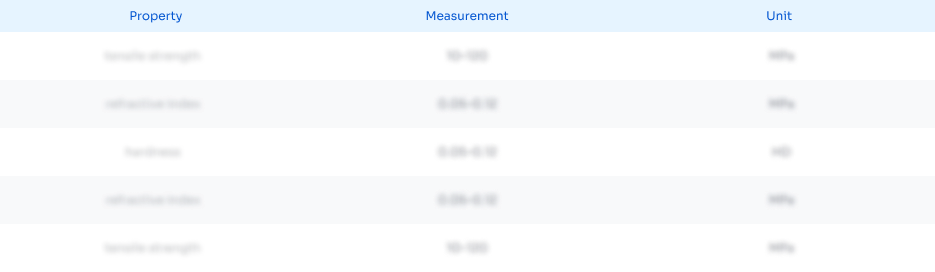
Abstract
Description
Claims
Application Information

- R&D
- Intellectual Property
- Life Sciences
- Materials
- Tech Scout
- Unparalleled Data Quality
- Higher Quality Content
- 60% Fewer Hallucinations
Browse by: Latest US Patents, China's latest patents, Technical Efficacy Thesaurus, Application Domain, Technology Topic, Popular Technical Reports.
© 2025 PatSnap. All rights reserved.Legal|Privacy policy|Modern Slavery Act Transparency Statement|Sitemap|About US| Contact US: help@patsnap.com