Chromium-free passivator with high corrosion resistance for batch hot galvanizing
A chrome-free passivator, high corrosion resistance technology, applied in hot dipping process, metal material coating process, coating and other directions, can solve problems such as high carcinogenicity and high toxicity, and achieve enhanced affinity and good stability , the effect of fast drying
- Summary
- Abstract
- Description
- Claims
- Application Information
AI Technical Summary
Problems solved by technology
Method used
Examples
Embodiment 1
[0036] The raw materials of each component are taken in the following mass percentages: 1% of silica sol, 0.3% of phosphoric acid, 2% of complexing agent, 5% of silane coupling agent, and the balance is deionized water.
[0037] Concretely make chromium-free passivating agent according to the following steps:
[0038] S11. Accurately weigh the raw materials of each component in the chromium-free passivator according to the mass percentage of each component in the chromium-free passivator;
[0039] S12. Put the silica sol, complexing agent, nitric acid, and silane coupling agent weighed in the above S11 into the reaction kettle according to the proportion, and mix and stir to obtain a mixed solution A;
[0040] S13. Add the phosphoric acid weighed in the above S11 into the mixed solution A, and continue stirring to obtain the mixed solution B;
[0041] S14. Add deionized water to the above mixed solution B, and mix thoroughly to obtain a mixed solution C, and then concentrate ...
Embodiment 2
[0044] The raw materials of each component are taken in the following mass percentages: 2% of silica sol, 0.4% of phosphoric acid, 4% of complexing agent, 6% of silane coupling agent, and the balance is deionized water.
[0045] Concretely make chromium-free passivating agent according to the following steps:
[0046] S11. Accurately weigh the raw materials of each component in the chromium-free passivator according to the mass percentage of each component in the chromium-free passivator;
[0047] S12. Put the silica sol, complexing agent, nitric acid, and silane coupling agent weighed in the above S11 into the reaction kettle according to the proportion, and mix and stir to obtain a mixed solution A;
[0048]S13. Add the phosphoric acid weighed in the above S11 into the mixed solution A, and continue stirring to obtain the mixed solution B;
[0049] S14. Add deionized water to the above mixed solution B, and mix thoroughly to obtain a mixed solution C, and then concentrate a...
Embodiment 3
[0051] The raw materials of each component are taken in the following mass percentages: 3% of silica sol, 0.5% of phosphoric acid, 5% of complexing agent, 7% of silane coupling agent, and the balance is deionized water.
[0052] Concretely make chromium-free passivating agent according to the following steps:
[0053] S11. Accurately weigh the raw materials of each component in the chromium-free passivator according to the mass percentage of each component in the chromium-free passivator;
[0054] S12. Put the silica sol, complexing agent, nitric acid, and silane coupling agent weighed in the above S11 into the reaction kettle according to the proportion, and mix and stir to obtain a mixed solution A;
[0055] S13. Add the phosphoric acid weighed in the above S11 into the mixed solution A, and continue stirring to obtain the mixed solution B;
[0056] S14. Add deionized water to the above mixed solution B, and mix thoroughly to obtain a mixed solution C, and then concentrate ...
PUM
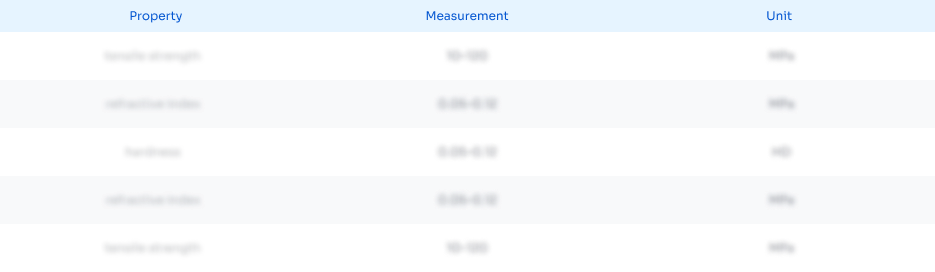
Abstract
Description
Claims
Application Information

- Generate Ideas
- Intellectual Property
- Life Sciences
- Materials
- Tech Scout
- Unparalleled Data Quality
- Higher Quality Content
- 60% Fewer Hallucinations
Browse by: Latest US Patents, China's latest patents, Technical Efficacy Thesaurus, Application Domain, Technology Topic, Popular Technical Reports.
© 2025 PatSnap. All rights reserved.Legal|Privacy policy|Modern Slavery Act Transparency Statement|Sitemap|About US| Contact US: help@patsnap.com