A process for preparing metal matrix ceramic composites by secondary pressure
A ceramic composite material and metal-based technology, which is applied in the technical field of preparing metal-based ceramic composite materials by secondary pressure, can solve the problem of low infiltration rate, achieve the effects of improving quality, compact structure, and avoiding adverse reactions
- Summary
- Abstract
- Description
- Claims
- Application Information
AI Technical Summary
Problems solved by technology
Method used
Image
Examples
specific Embodiment approach 1
[0090] The present invention needs to use manufacturing tool in manufacturing process, and its specific structure is as follows:
[0091] It mainly includes product forming mold assembly 2, sleeve mold 4, bottom plate 3, pressure head 9, secondary pressure plate 10 and so on.
[0092] The preheated product forming mold assembly 2 is placed on the bottom plate 3 in the cavity of the cover mold 4, and the base plate 3 with the product forming mold assembly 2 is placed on the workbench 6 in the cavity of the cover mold 4. The cover mold 4 and the working There is a sealing groove between the tables 6, between the press mandrel 5 and the workbench 6, and a sealing ring is placed for sealing. There is an air extraction channel 8 in the press mandrel 5, and a valve communicating with the air extraction channel 8 is provided in the middle of the bottom plate 3. The center hole 301, the press ejector rod 5 can drive the product forming mold assembly 2 to lift up and down in the cavity...
specific Embodiment approach 2
[0116] Embodiment 2: The difference between this embodiment and Embodiment 1 is that the ceramic reinforcement powder in the second step is diamond powder, the preheating temperature in the sixth step is 500-600°C, and the holding time is 3 hours. The specific embodiment one is the same.
specific Embodiment approach 3
[0117] Embodiment 3: The difference between this embodiment and Embodiment 1 is that the ceramic reinforcement powder in the second step is silicon carbide powder, the preheating temperature in the sixth step is 600-700°C, and the holding time is 4h. It is the same as the first embodiment.
PUM
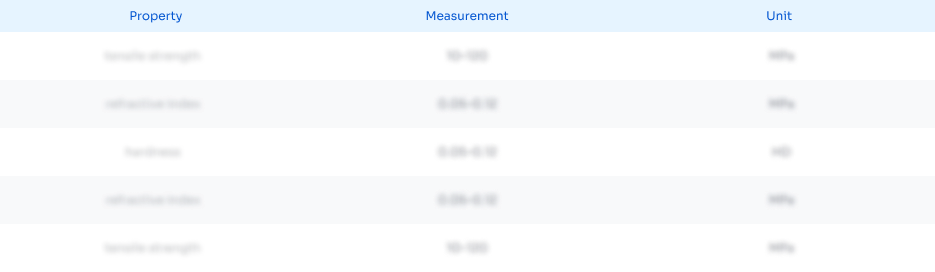
Abstract
Description
Claims
Application Information

- R&D
- Intellectual Property
- Life Sciences
- Materials
- Tech Scout
- Unparalleled Data Quality
- Higher Quality Content
- 60% Fewer Hallucinations
Browse by: Latest US Patents, China's latest patents, Technical Efficacy Thesaurus, Application Domain, Technology Topic, Popular Technical Reports.
© 2025 PatSnap. All rights reserved.Legal|Privacy policy|Modern Slavery Act Transparency Statement|Sitemap|About US| Contact US: help@patsnap.com