Method and device for realizing motor control based on FPGA
A motor control and computer program technology, applied in the field of signal processing, can solve the problems of medium separation or multiple separation, excessive friction between the separation components and the medium, and inability to achieve precise control.
- Summary
- Abstract
- Description
- Claims
- Application Information
AI Technical Summary
Problems solved by technology
Method used
Image
Examples
Embodiment Construction
[0062] In order to make the above objects, features and advantages of the present invention more comprehensible, the present invention will be further described in detail below in conjunction with the accompanying drawings and specific embodiments.
[0063] refer to figure 1 , shows a schematic structural view of media separation inside a container of the present invention, including a separation assembly 101, a detection assembly 102, a medium carrying assembly 103 and a motor 104; wherein, the separation assembly 101 is provided with a separation element 1011.
[0064] Wherein, the detection component 102 is used to judge the contact state between the medium and the separation element 1011. In one example, the detection component 102 can be an infrared sensor, and the infrared sensor emits infrared rays to the surface of the medium to judge the medium and the separation element 1011 according to the return of the infrared rays. The contact state of the separation element 101...
PUM
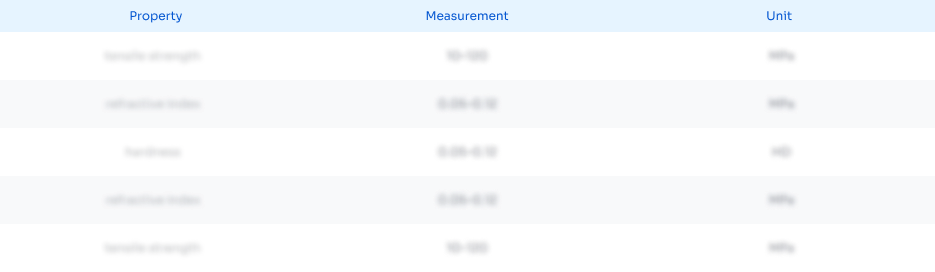
Abstract
Description
Claims
Application Information

- R&D
- Intellectual Property
- Life Sciences
- Materials
- Tech Scout
- Unparalleled Data Quality
- Higher Quality Content
- 60% Fewer Hallucinations
Browse by: Latest US Patents, China's latest patents, Technical Efficacy Thesaurus, Application Domain, Technology Topic, Popular Technical Reports.
© 2025 PatSnap. All rights reserved.Legal|Privacy policy|Modern Slavery Act Transparency Statement|Sitemap|About US| Contact US: help@patsnap.com