Oxygen-enriched and low-CO sintering method, oxygen-enriched and low-CO sintering machine and control method thereof
A sintering method and sintering machine technology, which are applied in furnaces, lighting and heating equipment, furnace types, etc., can solve the problems of high cost, large flue gas treatment capacity, and reduce the amount of CO generated in the sintering process, so as to reduce emissions and achieve The effect of low CO control and narrowing of the injection area
- Summary
- Abstract
- Description
- Claims
- Application Information
AI Technical Summary
Problems solved by technology
Method used
Image
Examples
Embodiment Construction
[0086] Please refer to Figure 6, Figure 7, Figure 6 is a schematic structural diagram of a cover body; Figure 7 is a B-B view of Figure 6.
[0093] Please refer to Figure 8, Figure 9, Figure 8 is a schematic structural diagram of the branch pipe row; Figure 9 is a cross-sectional view of the branch pipe row.
[0095] The end of the branch pipe row 16 is connected with the cover top hydraulic cylinder 27 through the pull rod 26, and the row of the cover top hydraulic cylinder 27 is adjusted by adjusting the cover top hydraulic cylinder 27.
[0102] Step 3: the C
[0108] Step 9: judge whether the valve still has a margin, if it executes step 10, if not, executes step 14;
[0110] Step 12: judge whether the hydraulic cylinder still has a margin, if so, execute step 13; if not, execute step 14;
[0112] Step 14: the program ends.
[0115] C+0.5O
[0116]CO+0.5O
[0118]
[0120]
[0122]
[0126] Q
[0128]
PUM
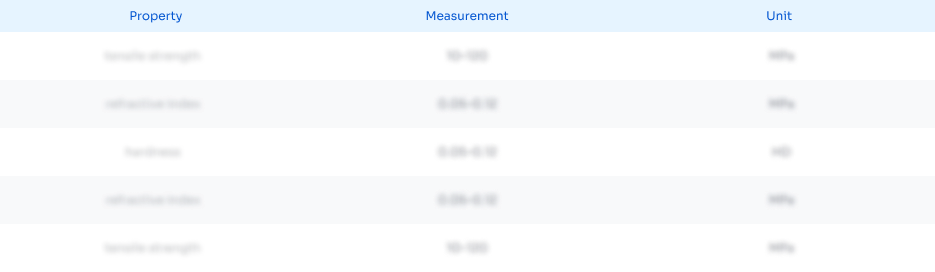
Abstract
Description
Claims
Application Information

- R&D
- Intellectual Property
- Life Sciences
- Materials
- Tech Scout
- Unparalleled Data Quality
- Higher Quality Content
- 60% Fewer Hallucinations
Browse by: Latest US Patents, China's latest patents, Technical Efficacy Thesaurus, Application Domain, Technology Topic, Popular Technical Reports.
© 2025 PatSnap. All rights reserved.Legal|Privacy policy|Modern Slavery Act Transparency Statement|Sitemap|About US| Contact US: help@patsnap.com