A flange seat, its manufacturing method, and hoisting machinery
A manufacturing method and flange seat technology are applied in the fields of hoisting machinery, flange seats and manufacturing, which can solve the problems of high labor intensity, low welding efficiency, large welding stress, etc., so as to reduce labor intensity and improve production efficiency. , The effect of reliable welding quality
- Summary
- Abstract
- Description
- Claims
- Application Information
AI Technical Summary
Problems solved by technology
Method used
Image
Examples
Embodiment 1
[0066] Such as Figure 4-Figure 7 As shown, the flange seat of this embodiment includes a bottom plate 3 , two lug plate assemblies, two sealing plates 4 and multiple rib plates 5 .
[0067] Let one of the length direction and the width direction of the bottom plate 3 be the X direction, and the other direction be the Y direction, and two ear plate assemblies are arranged on the bottom plate 3 and arranged at intervals along the X direction, as Figure 11 As shown, the bottom of the ear plate assembly is divided into N notch parts and N+1 socket parts 14 along its length direction, N≥1, and the bottom surface of the notch part is depressed upwards to form a groove that runs through the two walls of the ear plate in the thickness direction Mouth 11, such as Figure 12 As shown, the bottom plate 3 is provided with a through groove 31 that cooperates with the socket portion 14 of the ear plate assembly, and the socket portion 14 is clamped in the corresponding through groove 31 ...
Embodiment 2
[0074] In this embodiment, auxiliary tooling and auxiliary welding machines are used to complete the welding of the flange seat in embodiment 1. Among them, the auxiliary tooling includes a rotary tooling that makes each weld seam of the flange seat in a flat welding position, a clamp 7 for fixing the flange seat, and a limit structure 8 for preventing the deformation of the lug plate 1, and for preventing the deformation of the lug plate 1. The adornment shaft 9 that controls the coaxiality of the two hinge shaft holes 12 on the two ear plates 1. Among them, the rotary tooling includes a driving device 6, a working platform 61 connected to the driving device 6, and a clamp 7 connected to the working platform 61 for horizontal rotation, and the driving device 6 can drive the working platform 61 to turn vertically. The welded flange seat can drive the flange seat to rotate horizontally relative to the working platform 61 .
[0075] Such as Figure 13-16 Shown, the manufacturi...
PUM
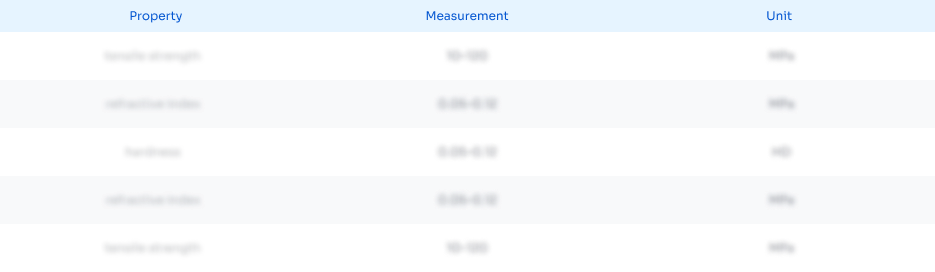
Abstract
Description
Claims
Application Information

- R&D
- Intellectual Property
- Life Sciences
- Materials
- Tech Scout
- Unparalleled Data Quality
- Higher Quality Content
- 60% Fewer Hallucinations
Browse by: Latest US Patents, China's latest patents, Technical Efficacy Thesaurus, Application Domain, Technology Topic, Popular Technical Reports.
© 2025 PatSnap. All rights reserved.Legal|Privacy policy|Modern Slavery Act Transparency Statement|Sitemap|About US| Contact US: help@patsnap.com