Prefabricated stand column
A column and pre-embedded technology, applied in the direction of columns, piers, pillars, etc., can solve the problems of low precision of prefabricated columns, inability to cover beams, small box beams and other problems, and achieve the effect of convenient insertion, reduced operation and good coordination.
- Summary
- Abstract
- Description
- Claims
- Application Information
AI Technical Summary
Problems solved by technology
Method used
Image
Examples
Embodiment 1
[0045] A prefabricated column such as Figures 1 to 3 As shown, it is formed by pouring concrete, including the bottom positioning plate 1 and the top embedded column sleeve 3, and the positioning plate 1 is fixedly connected with the grouting sleeve 2 (the internal structure of the grouting sleeve 2 is the prior art and will not be repeated here). The grouting sleeve is arranged near the outer edge of the positioning plate. The positioning plate 1 is provided with an opening corresponding to and connected to the grouting sleeve 2. Between the positioning plate 1 and the pre-embedded column sleeve 3, there are longitudinally arranged main ribs 7 and Annular stirrups 8 arranged along the cross section. The column is provided with a thickened stirrup section 9 and a standard stirrup section 10 in the axial direction, and the spacing between the adjacent annular stirrups 8 in the thickened stirrup section 9 is denser than that of the standard stirrup section 10. The rib densific...
Embodiment 2
[0051] This embodiment adds the following features on the basis of Embodiment 1:
[0052] Such as Image 6 , 7 , 8, the inner diameter of the middle part of the grouting sleeve 2 gradually increases from top to bottom, and a positioning piece is inserted in the grouting sleeve 2, and the positioning piece includes a positioning piece body 17 whose diameter is smaller than the inner diameter of the grouting sleeve 2 and 4 abutment pins 18 that are rotationally connected to the side wall of the locator body 17 in the circumferential direction. The side wall of the locator body 17 is provided with a concave ball seat 19, and the rotating end of the abutment pin 18 is inserted into the concave There is a gap between the ball seat 19 and the concave ball seat 19; the locator moves in one direction on the grouting sleeve 2:
[0053] When the positioning piece is inserted into the grouting sleeve 2 from bottom to top, the abutment pin 18 rotates and retracts toward the axis of the ...
Embodiment 3
[0061] On the basis of embodiment 2, it also has the following characteristics:
[0062] Such as Figure 9 As shown, the concave ball seat 19 is provided with an elastic block 20, and the elastic block 20 drives the abutment pin 18 to expand in the radial direction of the positioning member. Overcome the elastic piece when inserting the positioning piece. When inserting the main rib 7, the elastic block 20 drives the abutment pin 18 to expand, and the effect of one-way movement is better.
PUM
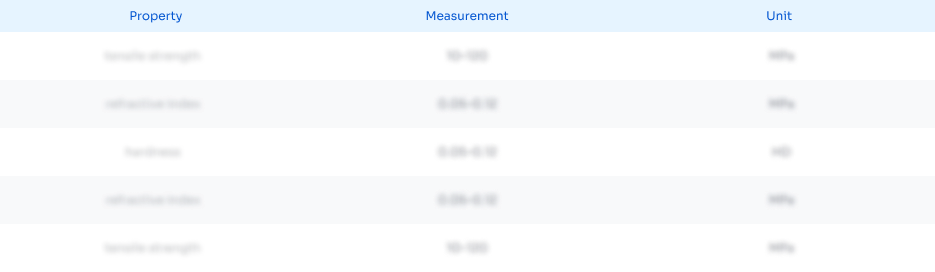
Abstract
Description
Claims
Application Information

- Generate Ideas
- Intellectual Property
- Life Sciences
- Materials
- Tech Scout
- Unparalleled Data Quality
- Higher Quality Content
- 60% Fewer Hallucinations
Browse by: Latest US Patents, China's latest patents, Technical Efficacy Thesaurus, Application Domain, Technology Topic, Popular Technical Reports.
© 2025 PatSnap. All rights reserved.Legal|Privacy policy|Modern Slavery Act Transparency Statement|Sitemap|About US| Contact US: help@patsnap.com