Water-lubricated bearing composite material and preparation method thereof
A technology of water-lubricated bearings and composite materials, which is applied in the field of composite materials and can solve problems such as poor wear resistance
- Summary
- Abstract
- Description
- Claims
- Application Information
AI Technical Summary
Problems solved by technology
Method used
Image
Examples
preparation example Construction
[0023] The invention provides a method for preparing a water-lubricated bearing composite material, comprising the following steps:
[0024] Mix toluene diisocyanate (TDI) and polytetramethylene glycol for addition reaction to obtain PU prepolymer;
[0025] Mixing the PU prepolymer, epoxy resin and a first organic solvent to obtain a first compound;
[0026] The nitrile rubber is mixed with the second organic solvent to obtain the nitrile rubber solution;
[0027] The first mixture, nitrile rubber solution, additives, vulcanization aids, anti-aging agent D, vulcanizing agent and curing agent are mixed and dried to obtain a premix;
[0028] The premixed material is sequentially kneaded, vulcanized and solidified to obtain the water-lubricated bearing composite material.
[0029] The invention mixes toluene diisocyanate (TDI) and polytetramethylene glycol for addition reaction to obtain PU prepolymer.
[0030] In the present invention, the polytetramethylene glycol is prefera...
Embodiment 1
[0064] Cut 30g of NBR raw rubber into small pieces and dissolve in 300g of THF, and stir vigorously; at the same time, dissolve 12g of PU prepolymer and 6g of E51 in 180g of chloroform, and after the NBR raw rubber is completely dissolved, Pour the chloroform mixed solution of PU prepolymer and E51 into the above-mentioned NBR solution, stir vigorously for 24h, mix carbon black (consumption is 60wt% of nitrile rubber), stearic acid (consumption is 1wt% of nitrile rubber) ), zinc oxide (consumption is 3wt% of nitrile rubber), vulcanization accelerator TMTD (consumption is 0.7wt% of nitrile rubber), vulcanization accelerator MBT (consumption is 0.53wt% of nitrile rubber), vulcanization accelerator CTP (consumption is 0.53wt% of nitrile rubber), vulcanization accelerator CZ (consumption is 0.2wt% of nitrile rubber), antioxidant D (consumption is 1wt% of nitrile rubber), sulfur (consumption is nitrile rubber 2wt%), curing agent MOCA (the amount is 15.37wt% of the total amount of P...
Embodiment 2
[0066] Cut 30g of NBR raw rubber into small pieces and dissolve it in 300g of THF, and stir vigorously; at the same time, dissolve 12g of PU prepolymer and 9g of E51 in 180g of chloroform, and after the NBR raw rubber is completely dissolved, Pour the chloroform mixed solution of PU prepolymer and E51 into the above-mentioned NBR solution, stir vigorously for 24h, mix carbon black (consumption is 60wt% of nitrile rubber), stearic acid (consumption is 1wt% of nitrile rubber) ), zinc oxide (consumption is 3wt% of nitrile rubber), vulcanization accelerator TMTD (consumption is 0.7wt% of nitrile rubber), vulcanization accelerator MBT (consumption is 0.53wt% of nitrile rubber), vulcanization accelerator CTP (consumption is 0.53wt% of nitrile rubber), vulcanization accelerator CZ (consumption is 0.2wt% of nitrile rubber), antioxidant D (consumption is 1wt% of nitrile rubber), sulfur (consumption is nitrile rubber 2wt%), curing agent MOCA (the amount is 18.04wt% of the total amount o...
PUM
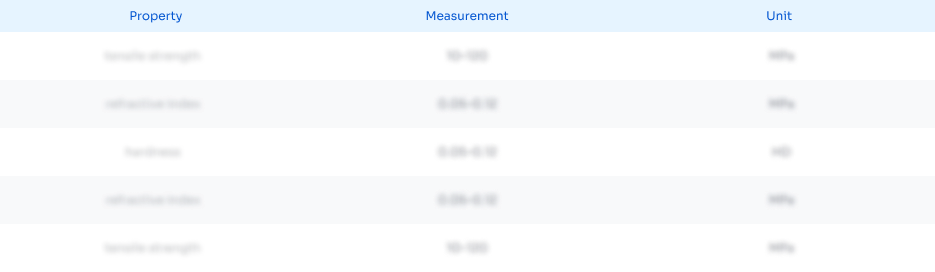
Abstract
Description
Claims
Application Information

- R&D
- Intellectual Property
- Life Sciences
- Materials
- Tech Scout
- Unparalleled Data Quality
- Higher Quality Content
- 60% Fewer Hallucinations
Browse by: Latest US Patents, China's latest patents, Technical Efficacy Thesaurus, Application Domain, Technology Topic, Popular Technical Reports.
© 2025 PatSnap. All rights reserved.Legal|Privacy policy|Modern Slavery Act Transparency Statement|Sitemap|About US| Contact US: help@patsnap.com