Manufacturing method of high-wear-resistance rubber steel wire hose and mold forming device
A technology for steel wire hoses and manufacturing methods, which can be applied to adhesives, tubular objects, household appliances, etc., can solve problems affecting the quality of hoses, overflow, etc., and achieve the effects of reducing energy consumption, improving performance, and improving bonding strength
- Summary
- Abstract
- Description
- Claims
- Application Information
AI Technical Summary
Problems solved by technology
Method used
Image
Examples
Embodiment 1
[0109] A method for manufacturing a high wear-resistant rubber steel wire elbow hose, comprising the following steps:
[0110] A. Film preprocessing:
[0111] The wear-resistant rubber layer adopts the following formula: 100 parts of natural rubber; 15 parts of carbon black N220; 30 parts of carbon black N330; 10 parts of aromatic oil; 3 parts of anti-aging agent RD, 4 parts of anti-aging agent BLE; 4 parts of zinc oxide; 1 part stearic acid; 2 parts sulfur; 1 part accelerator NOBS.
[0112] The inner weather-resistant layer and the outer weather-resistant layer can adopt the following formula: 70 parts of natural rubber; 30 parts of EPDM rubber; 50 parts of carbon black N774; 12 parts of naphthenic oil; 1.5 parts of anti-aging agent RD; 23 parts of anti-aging agent 4010NA ; 2 parts of dispersant WB212; 3 parts of zinc oxide; 3 parts of stearic acid; 1.6 parts of sulfur; 1.8 parts of accelerator NOBS.
[0113] The adhesive can adopt the following formula: 100 parts of neopre...
Embodiment 2
[0135] A method for manufacturing a high wear-resistant rubber steel wire elbow hose, comprising the following steps:
[0136] A. Film pretreatment: Weigh the raw materials of wear-resistant layer, weather-resistant layer and adhesive glue respectively;
[0137] The wear-resistant rubber layer adopts the following formula: 100 parts of natural rubber; 15 parts of carbon black N220; 30 parts of carbon black N330; 10 parts of aromatic oil; 3 parts of anti-aging agent RD, 4 parts of anti-aging agent BLE; 4 parts of zinc oxide; 1 part stearic acid; 2 parts sulfur; 1 part accelerator NOBS.
[0138] The weather-resistant layer includes the following raw materials in parts by weight: 60 parts of natural rubber; 20 parts of EPDM rubber; 40 parts of carbon black N774, 10 parts of naphthenic oil; 1 part of anti-aging agent RD; 1 part of anti-aging agent 4010NA; Parts of dispersant WB212; 2 parts of zinc oxide; 2 parts of stearic acid; 1 part of sulfur; 0.6 parts of accelerator NOBS.
...
Embodiment 3
[0152] A method for manufacturing a high wear-resistant rubber steel wire elbow hose, comprising the following steps:
[0153] A. Film pretreatment: Weigh the raw materials of wear-resistant layer, weather-resistant layer and adhesive glue respectively;
[0154] The wear-resistant rubber layer adopts the following formula: 100 parts of natural rubber; 15 parts of carbon black N220; 30 parts of carbon black N330; 10 parts of aromatic oil; 3 parts of anti-aging agent RD, 4 parts of anti-aging agent BLE; 4 parts of zinc oxide; 1 part stearic acid; 2 parts sulfur; 1 part accelerator NOBS.
[0155]The weather-resistant layer includes the following raw materials in parts by weight: 80 parts of natural rubber; 40 parts of EPDM; 60 parts of carbon black N774, 15 parts of naphthenic oil; 2 parts of antioxidant RD; 3 parts of antioxidant 4010NA; Parts of dispersant WB212; 4 parts of zinc oxide; 4 parts of stearic acid; 2 parts of sulfur; 1 part of accelerator NOBS.
[0156] The adhesi...
PUM
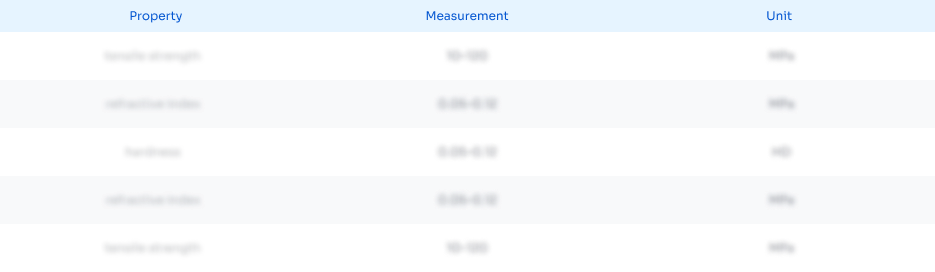
Abstract
Description
Claims
Application Information

- Generate Ideas
- Intellectual Property
- Life Sciences
- Materials
- Tech Scout
- Unparalleled Data Quality
- Higher Quality Content
- 60% Fewer Hallucinations
Browse by: Latest US Patents, China's latest patents, Technical Efficacy Thesaurus, Application Domain, Technology Topic, Popular Technical Reports.
© 2025 PatSnap. All rights reserved.Legal|Privacy policy|Modern Slavery Act Transparency Statement|Sitemap|About US| Contact US: help@patsnap.com