Maximum torque current ratio control method for built-in permanent magnet synchronous motor
A permanent magnet synchronous motor, maximum torque current technology, applied in motor generator control, electronic commutation motor control, control system and other directions, can solve problems such as slow convergence speed, poor convergence performance and dynamic performance, and poor dynamic performance , to achieve the effect of improving dynamic performance, fast MTPA control, and improving startup performance
- Summary
- Abstract
- Description
- Claims
- Application Information
AI Technical Summary
Problems solved by technology
Method used
Image
Examples
Embodiment Construction
[0062] In order to make the technical solutions and advantages of the present invention more clear, the technical solutions in the embodiments of the present invention are clearly and completely described below in conjunction with the drawings in the embodiments of the present invention:
[0063] Such as figure 1 As shown, the present invention discloses a method for controlling the maximum torque-to-current ratio of a built-in permanent magnet synchronous motor, which specifically includes the following steps:
[0064] S1: According to the mathematical model of the built-in permanent magnet synchronous motor and the Lagrangian extreme value theorem, the dq axis current formula is derived;
[0065] S2: According to the further simplification of the dq-axis current relationship, redefine a variable i K , deduce dq axis current and i K The relationship between;
[0066] S3: According to the mathematical model of the built-in permanent magnet synchronous motor in the synchrono...
PUM
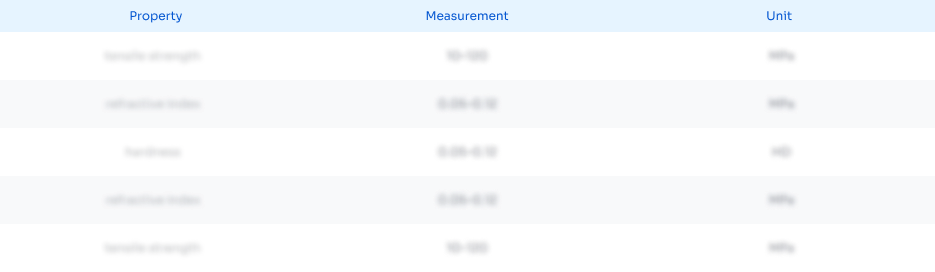
Abstract
Description
Claims
Application Information

- Generate Ideas
- Intellectual Property
- Life Sciences
- Materials
- Tech Scout
- Unparalleled Data Quality
- Higher Quality Content
- 60% Fewer Hallucinations
Browse by: Latest US Patents, China's latest patents, Technical Efficacy Thesaurus, Application Domain, Technology Topic, Popular Technical Reports.
© 2025 PatSnap. All rights reserved.Legal|Privacy policy|Modern Slavery Act Transparency Statement|Sitemap|About US| Contact US: help@patsnap.com