High-thermal-conductivity graphene film and preparation method thereof
A high thermal conductivity graphite and graphene film technology, applied in the field of thermal conductive materials, can solve the problems of heavy metal film, low thermal conductivity, and large time consumption.
- Summary
- Abstract
- Description
- Claims
- Application Information
AI Technical Summary
Problems solved by technology
Method used
Image
Examples
Embodiment 1
[0032] ①Mix 6g of graphene oxide and 24g of hardwood fiber raw materials, and dilute the mixed slurry with water to a concentration of 10%. The mass of graphene oxide accounts for 20% of the total mass of fiber raw materials and graphene oxide, and mix them into a PFI disc refiner Refining is carried out to obtain a mixed slurry of graphene oxide and fibers, and the degree of beating is 45°SR.
[0033] ②①Add 15g of polyvinyl alcohol to the prepared mixed slurry, the mass concentration of the added polyvinyl alcohol is 5%, and carry out vacuum filtration to obtain a graphene oxide film (GO film).
[0034] ③Put the GO film prepared in ② into a vacuum drying oven to dry for 2 hours to obtain a dried GO film at a drying temperature of 80°C;
[0035] ④ Put the dried GO film obtained in ③ into a tube furnace for carbonization treatment. During the carbonization process, first raise the temperature to 300°C, keep it for 40 minutes, continue to raise the temperature to 500°C, keep it ...
Embodiment 2
[0040] ①Mix 12g of graphene oxide and 18g of hardwood fiber raw materials, and dilute the mixed slurry with water to a concentration of 10%. The mass of graphene oxide accounts for 40% of the total mass of fiber raw materials and graphene oxide, and mix them into a PFI disc refiner Refining is carried out to obtain a mixed slurry of graphene oxide and fibers, and the degree of beating is 45°SR.
[0041] ②① Add 15 g of polyvinyl alcohol to the prepared mixed slurry, and add polyvinyl alcohol with a mass concentration of 5%, and perform vacuum filtration to obtain a graphene oxide film (GO film).
[0042] ③Put the GO film prepared in ② into a vacuum drying oven to dry for 2 hours to obtain a dried GO film at a drying temperature of 80°C;
[0043] ④ Put the dried GO film obtained in ③ into a tube furnace for carbonization treatment. During the carbonization process, first raise the temperature to 300°C, keep it for 40 minutes, continue to raise the temperature to 500°C, keep it f...
Embodiment 3
[0047] ①Mix 18g of graphene oxide and 12g of hardwood fiber raw material, dilute the mixed slurry with water to a concentration of 10%, the mass of graphene oxide accounts for 60% of the total mass of fiber raw material and graphene oxide, mix and put into PFI disc mill The machine is used for refining to obtain a mixed slurry of graphene oxide and fiber, and the degree of beating is 45°SR.
[0048] ②①Add 18g of polyvinyl alcohol to the prepared mixed slurry, the mass concentration of the added polyvinyl alcohol is 6%, and carry out vacuum filtration to obtain a graphene oxide film (GO film).
[0049] ③Put the GO film prepared in ② into a vacuum drying oven to dry for 2 hours to obtain a dried GO film at a drying temperature of 80°C;
[0050] ④ Put the dried GO film obtained in ③ into a tube furnace for carbonization treatment. During the carbonization process, first raise the temperature to 300°C, keep it for 30 minutes, continue to raise the temperature to 500°C, keep it for 3...
PUM
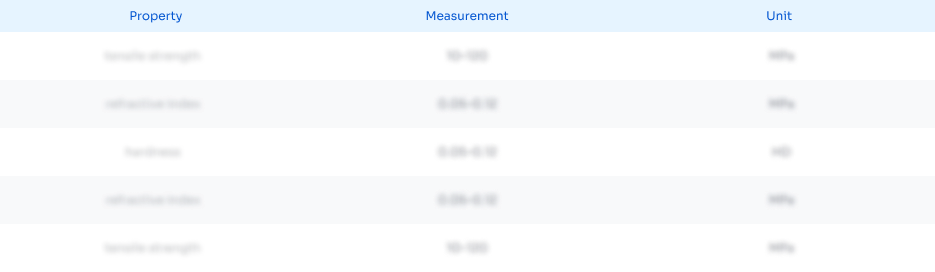
Abstract
Description
Claims
Application Information

- R&D
- Intellectual Property
- Life Sciences
- Materials
- Tech Scout
- Unparalleled Data Quality
- Higher Quality Content
- 60% Fewer Hallucinations
Browse by: Latest US Patents, China's latest patents, Technical Efficacy Thesaurus, Application Domain, Technology Topic, Popular Technical Reports.
© 2025 PatSnap. All rights reserved.Legal|Privacy policy|Modern Slavery Act Transparency Statement|Sitemap|About US| Contact US: help@patsnap.com