Lubricant for drilling fluid and preparation method thereof
A lubricant and drilling fluid technology, applied in the field of lubricant preparation, can solve the problems of limited lubricating effect, poor temperature resistance, low extreme pressure film strength, etc., and achieve the effect of improving the lubricating effect, reducing the amount of wear and avoiding direct contact
- Summary
- Abstract
- Description
- Claims
- Application Information
AI Technical Summary
Problems solved by technology
Method used
Image
Examples
Embodiment 1
[0039] Mix zinc nitrate, thiourea, diethylenetriamine and distilled water at a molar ratio of 1:1:6:55 and put them into a stainless steel reactor with a polytetrafluoroethylene liner, seal it, and let it stand at 170°C The crystallization reaction was carried out for 10 hours. After the reaction was completed, the filter residue was obtained by washing, centrifuging, and filtering, and dried at 100°C to constant weight to obtain lubricated microspheres;
[0040] In parts by weight, take 3 parts of lubricated microspheres, 6 parts of colloidal graphite, and 10 parts of RDX and mix them into a high-pressure airtight container, and fill the high-pressure airtight container with a volume ratio of 3:1 nitrogen and argon. After detonating the mixed gas with a lead wire, let it stand for 10 minutes, and collect the carbon-coated lubricating microsphere particles;
[0041] Add 1-aminopropyl-3-methylimidazolium bromide and triethanolamine into a round-bottomed flask at a mass ratio of...
Embodiment 2
[0045] Mix zinc nitrate, thiourea, diethylenetriamine and distilled water at a molar ratio of 1:1:6:55, put them into a stainless steel reactor with a polytetrafluoroethylene liner, seal it, and let it stand at 175°C The crystallization reaction was carried out for 11 hours. After the reaction was completed, the filter residue was obtained by washing, centrifuging, and filtering, and dried at 103°C to constant weight to obtain lubricated microspheres;
[0046] In parts by weight, take 4 parts of lubricated microspheres, 6 parts of colloidal graphite, and 11 parts of black sogen and mix them into a high-pressure airtight container, and fill the high-pressure airtight container with a volume ratio of 3:1 nitrogen and argon. After detonating the mixed gas with a lead wire, let it stand for 13 minutes, and collect the carbon-coated lubricating microsphere particles;
[0047] Add 1-aminopropyl-3-methylimidazolium bromide and triethanolamine into a round-bottomed flask at a mass rat...
Embodiment 3
[0051] Mix zinc nitrate, thiourea, diethylenetriamine and distilled water at a molar ratio of 1:1:6:55, put them into a stainless steel reaction kettle with a polytetrafluoroethylene liner, seal it, and let it stand at 180°C The crystallization reaction was carried out for 12 hours. After the reaction was completed, the filter residue was obtained by washing, centrifuging, and filtering, and dried at 105°C to constant weight to obtain lubricated microspheres;
[0052] In parts by weight, take 5 parts of lubricated microspheres, 7 parts of colloidal graphite, and 12 parts of black sogen and mix them into a high-pressure airtight container, and fill the high-pressure airtight container with a volume ratio of 3:1 nitrogen and argon. After detonating the mixed gas with a lead wire, let it stand for 15 minutes, and collect the carbon-coated lubricating microsphere particles;
[0053] Add 1-aminopropyl-3-methylimidazolium bromide and triethanolamine into a round-bottomed flask at a ...
PUM
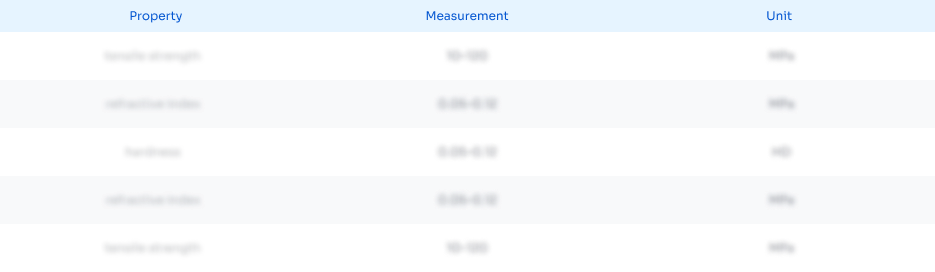
Abstract
Description
Claims
Application Information

- R&D Engineer
- R&D Manager
- IP Professional
- Industry Leading Data Capabilities
- Powerful AI technology
- Patent DNA Extraction
Browse by: Latest US Patents, China's latest patents, Technical Efficacy Thesaurus, Application Domain, Technology Topic, Popular Technical Reports.
© 2024 PatSnap. All rights reserved.Legal|Privacy policy|Modern Slavery Act Transparency Statement|Sitemap|About US| Contact US: help@patsnap.com