Preparation method of 2-R1 valeric acid
A technology of 2-R1 and valeric acid, which is applied in the field of preparation of 2-R1 valeric acid, can solve problems such as harsh conditions and dangerous operation, and achieve the effects of short synthesis route, easy control, and avoiding ultra-high temperature or ultra-low temperature
- Summary
- Abstract
- Description
- Claims
- Application Information
AI Technical Summary
Problems solved by technology
Method used
Image
Examples
Embodiment 1
[0032] 1.1 Preparation of methyl 2-cyanovalerate
[0033] Add 720g of methyl cyanoacetate, 1140g of methanol, 714g (0.8eq) equivalent of bromopropane in the reaction flask, raise the temperature to 50 degrees, and add dropwise 784g of a mass concentration of 30% sodium methoxide methanol solution (sodium methoxide 0.6 eq), controlled reaction temperature 50~60 degree, refluxed 1 hour, normal pressure distilled methanol, then reduced pressure distilled methanol to dryness to obtain crude product 1268g. Add 800 ml of isopropyl acetate, beat and filter to remove salt, and wash the obtained isopropyl acetate phase with 500 ml*6 of 5% sodium hydroxide aqueous solution until the methyl cyanoacetate is less than 0.5%, and add 500 ml of concentration to the oil phase Wash once with 1% sulfuric acid aqueous solution, then add 500 milliliters of water and wash once to neutrality, and concentrate the oil phase to dryness to obtain crude product 360g (compound B is 76%, compound C is 20%)...
Embodiment 2
[0042] 2.1 Preparation of methyl 2-cyanovalerate
[0043] Add 720g of methyl cyanoacetate, 1140g of methanol, 892g (1.0eq) equivalent bromopropane in the reaction flask, raise the temperature to 50 degrees, and add dropwise 1041g of a mass concentration of 30% sodium methoxide methanol solution (sodium methoxide 0.8 eq), controlled reaction temperature 50~60 degree, refluxed 1 hour, normal pressure distilled methanol, then reduced pressure distilled methanol to dryness to obtain crude product 1268g. Add 800 ml of isopropyl acetate, beat and filter to remove salt, wash the obtained isopropyl acetate phase with 500 ml*6 of 5% sodium hydroxide aqueous solution until the methyl cyanoacetate is less than 0.5%, add 500 ml of concentration to the oil phase Wash once with 1% sulfuric acid aqueous solution, then add 500 milliliters of water and wash once to neutrality, and concentrate the oil phase to dryness to obtain crude product 360g (compound B is 76%, compound C is 20%), using a ...
Embodiment 3
[0052] 3.1 Preparation of methyl 2-cyanovalerate
[0053] Add 720g of methyl cyanoacetate, 1140g of methanol, 892.5g (1.0eq) of equivalent bromopropane in the reaction flask, heat up to a temperature of 50 degrees, and add dropwise 1306g of a mass concentration of 30% sodium methoxide methanol solution (sodium methoxide 1.0eq), control the reaction temperature at 45-55 degrees, reflux for 1 hour, distill methanol under normal pressure, then distill methanol under reduced pressure to dryness to obtain 1300g of crude product. Add 800 ml of isopropyl acetate, beat and filter to remove salt, wash the obtained isopropyl acetate phase with 500 ml*6 of 5% sodium hydroxide aqueous solution until the methyl cyanoacetate is less than 0.5%, add 500 ml of concentration to the oil phase Wash once with 1% sulfuric acid aqueous solution, then add 500 milliliters of water and wash once to neutrality, and concentrate the oil phase to dryness to obtain 400 g of crude product (compound B is 76%,...
PUM
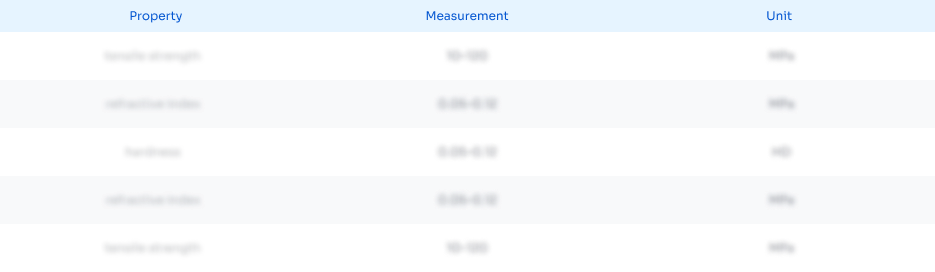
Abstract
Description
Claims
Application Information

- Generate Ideas
- Intellectual Property
- Life Sciences
- Materials
- Tech Scout
- Unparalleled Data Quality
- Higher Quality Content
- 60% Fewer Hallucinations
Browse by: Latest US Patents, China's latest patents, Technical Efficacy Thesaurus, Application Domain, Technology Topic, Popular Technical Reports.
© 2025 PatSnap. All rights reserved.Legal|Privacy policy|Modern Slavery Act Transparency Statement|Sitemap|About US| Contact US: help@patsnap.com