Copper-containing catalyst as well as preparation method and application thereof
A copper catalyst and catalyst technology, applied in the field of coatings, can solve problems such as not provided, and achieve the effects of improving flexibility, solving slow drying speed, and simple operation
- Summary
- Abstract
- Description
- Claims
- Application Information
AI Technical Summary
Problems solved by technology
Method used
Image
Examples
Embodiment 1
[0070] (1) Preparation of cellulose oxide containing aldehyde groups
[0071] Weigh 5.0 g of microcrystalline cellulose, place it in a three-necked flask, add 200 mL of 0.1 mol / L sodium periodate solution, stir in the dark at a constant temperature of 50 ° C, and oxidize for 1.5 h. The product is suction filtered, washed with ethanol, Vacuum drying at 30°C for 24 hours to obtain cellulose oxide containing aldehyde groups.
[0072] (2) Preparation of cellulose-based Schiff base ligands
[0073] Weigh 1.08g of p-phenylenediamine and dissolve it in 30mL ethanol aqueous solution (ethanol: water = 1:2, volume ratio). After it is completely dissolved, add 0.8g of microcrystalline cellulose and continue stirring for 1h at a constant temperature of 60°C. After Schiff base reaction, the product was subjected to suction filtration, washed with ethanol, and dried in vacuum at 30°C for 24 hours to obtain the cellulose-based Schiff base ligand.
[0074] (3) Preparation of cellulose-based...
Embodiment 2
[0077] (1) Preparation of cellulose oxide containing aldehyde groups
[0078] Weigh 5.0 g of microcrystalline cellulose, place it in a three-necked flask, add 200 mL of 0.1 mol / L sodium periodate solution, stir in the dark at a constant temperature of 60 ° C, and oxidize for 1 h. ℃ vacuum drying for 24 hours to prepare cellulose oxide containing aldehyde groups.
[0079] (2) Preparation of cellulose-based Schiff base ligands
[0080] Weigh 1.2g of p-phenylenediamine and dissolve it in 36mL of ethanol aqueous solution (ethanol: water = 1:2, volume ratio). After it is completely dissolved, add 0.8g of microcrystalline cellulose and continue stirring for 1h at a constant temperature of 60°C. After Schiff base reaction, the product was subjected to suction filtration, washed with ethanol, and dried in vacuum at 30°C for 24 hours to obtain the cellulose-based Schiff base ligand.
[0081] (3) Preparation of cellulose-based Schiff base copper complexes
[0082] Weigh 0.6g of anhyd...
Embodiment 3
[0084] (1) Preparation of cellulose oxide containing aldehyde groups
[0085] Weigh 5.0 g of microcrystalline cellulose, place it in a three-necked flask, add 200 mL of 0.1 mol / L sodium periodate solution, stir at a constant temperature of 70 °C in the dark, and oxidize for 0.5 h. The product is suction filtered, washed with ethanol, Vacuum drying at 30°C for 24 hours to obtain aldehyde-containing cellulose oxide.
[0086] (2) Preparation of cellulose-based Schiff base ligands
[0087] Weigh 1.5g of p-phenylenediamine and dissolve it in 50mL ethanol aqueous solution (ethanol: water = 1:2, volume ratio). After it is completely dissolved, add 0.8g of microcrystalline cellulose and continue stirring for 1h at a constant temperature of 60°C. After Schiff base reaction, the product was subjected to suction filtration, washed with ethanol, and dried in vacuum at 30°C for 24 hours to obtain the cellulose-based Schiff base ligand.
[0088] (3) Preparation of cellulose-based Schiff b...
PUM
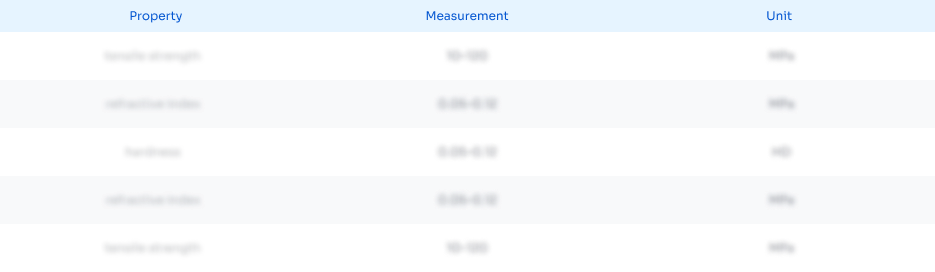
Abstract
Description
Claims
Application Information

- Generate Ideas
- Intellectual Property
- Life Sciences
- Materials
- Tech Scout
- Unparalleled Data Quality
- Higher Quality Content
- 60% Fewer Hallucinations
Browse by: Latest US Patents, China's latest patents, Technical Efficacy Thesaurus, Application Domain, Technology Topic, Popular Technical Reports.
© 2025 PatSnap. All rights reserved.Legal|Privacy policy|Modern Slavery Act Transparency Statement|Sitemap|About US| Contact US: help@patsnap.com