Waste heat recovery device of aluminum alloy smelting furnace
A waste heat recovery device and aluminum alloy technology, which is applied in the field of aluminum alloy melting furnaces, can solve the problems that heat cannot be recycled and utilized
- Summary
- Abstract
- Description
- Claims
- Application Information
AI Technical Summary
Problems solved by technology
Method used
Image
Examples
Embodiment Construction
[0028] The implementation manner of the present application will be further described in detail below with reference to the drawings and embodiments. The following examples are used to illustrate the present application, but cannot be used to limit the scope of the present application.
[0029] Such as figure 1 As shown, in the embodiment of the present application, an aluminum alloy melting furnace waste heat recovery device is provided, including a tail gas collection pipe 100 and a heat exchange pipe 200, the inlet of the tail gas collection pipe 100 is located above the opening of the swirl chamber 800, and the tail gas is The tube 100 is sleeved on the outside of the heat exchange tube 200, one end of the heat exchange tube 200 extends to the inlet of the exhaust gas collection tube 100 and is located outside the exhaust gas collection tube 100, and the other end of the heat exchange tube 200 communicates with the interior of the furnace body 700 ; The exhaust gas collec...
PUM
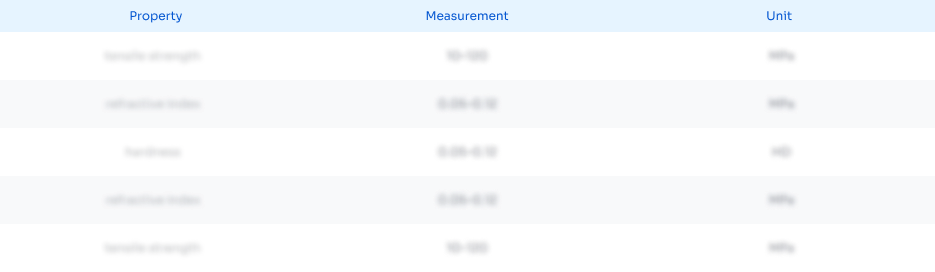
Abstract
Description
Claims
Application Information

- R&D Engineer
- R&D Manager
- IP Professional
- Industry Leading Data Capabilities
- Powerful AI technology
- Patent DNA Extraction
Browse by: Latest US Patents, China's latest patents, Technical Efficacy Thesaurus, Application Domain, Technology Topic, Popular Technical Reports.
© 2024 PatSnap. All rights reserved.Legal|Privacy policy|Modern Slavery Act Transparency Statement|Sitemap|About US| Contact US: help@patsnap.com