Catalyst for methane-hydrogen sulfide reforming hydrogen production process, and regeneration method thereof
A catalyst and sulfide technology, which is applied in the field of catalyst and its regeneration in the process of methane-hydrogen sulfide reforming hydrogen production, can solve the problems of no catalyst regeneration method, no development, etc.
- Summary
- Abstract
- Description
- Claims
- Application Information
AI Technical Summary
Problems solved by technology
Method used
Image
Examples
Embodiment 1
[0124] Al at a concentration of 10g / L 2 (SO 4 ) 3 1L of solution is used as the raw material, and NaAlO with a concentration of 10g / L is added dropwise while stirring in a water bath at 25°C. 2 Solution, when the pH of the mixed solution=8.0, stop dripping and stirring, then let it stand for 12 hours, then add MgSO with a concentration of 5g / L 4 3L of the solution and 1g of sodium lauryl sulfate powder were placed in an ultrasonic oscillator for 6 hours of shaking. The shaken mixture was filtered, and the filter cake was washed with deionized water. Take out the filter cake, put it into absolute ethanol liquid and soak for 1 hour, and then obtain the filter cake after filtering. Put the filter cake in a fume hood to air-dry for 12 hours, then put it in a 120°C oven for 12 hours, then transfer it to a high-temperature muffle furnace, raise the temperature to 800°C at a rate of 2°C / min, and keep it at a constant temperature for 12 hours. After cooling get MgAl 2 o 4 sampl...
Embodiment 2
[0127] Al with a concentration of 60g / L 2 (SO 4 ) 3 1L of solution is used as the raw material, and NaAlO with a concentration of 60g / L is added dropwise while stirring under the condition of a water bath at 85°C. 2 Solution, when the pH of the mixed solution=8.0, stop the dripping and stirring, then cool and stand for 12 hours, then add MgSO with a concentration of 55g / L 4 Solution 3L, and sodium lauryl sulfate powder 50g, then put it into an ultrasonic oscillator and vibrate for 6 hours. Filter the shaken mixture, wash the filter cake with deionized water, take out the filter cake, soak it in absolute ethanol liquid for 12 hours, and obtain the filter cake after filtering. Put the filter cake in a fume hood to air-dry for 12 hours, then put it in a 120°C oven to dry for 12 hours, then transfer it to a high-temperature muffle furnace, raise the temperature to 1200°C at a rate of 2°C / min, and keep it at a constant temperature for 12 hours. After cooling get MgAl 2 o 4 sa...
Embodiment 3
[0130] Al at a concentration of 40g / L 2 (SO 4 ) 3 1L of solution is used as the raw material, and NaAlO with a concentration of 50g / L is added dropwise while stirring in a water bath at 65°C. 2 solution, when the pH of the mixed solution = 8.0, stop dripping and stirring, then let it stand for 12 hours, and add MgSO with a concentration of 45g / L 4 Solution 3L, and sodium lauryl sulfate powder 20g, put into the ultrasonic oscillator and vibrate for 6 hours, wash the filter cake with deionized water after filtering, put the filter cake into absolute ethanol liquid and soak for 8 hours, filter and put The filter cake was air-dried in a fume hood for 12 hours, then dried in an oven at 120°C for 12 hours, then transferred to a high-temperature muffle furnace, heated to 1000°C at a rate of 2°C / min, kept at a constant temperature for 12 hours, and obtained after cooling MgAl 2 o 4 Sample, the sample is soaked in the weight concentration of 20% ethylene glycol aqueous solution, f...
PUM
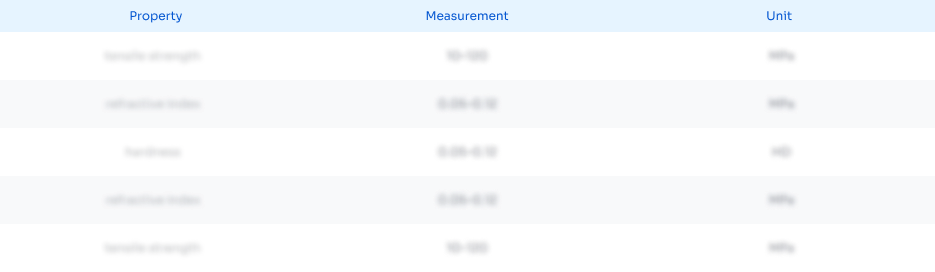
Abstract
Description
Claims
Application Information

- Generate Ideas
- Intellectual Property
- Life Sciences
- Materials
- Tech Scout
- Unparalleled Data Quality
- Higher Quality Content
- 60% Fewer Hallucinations
Browse by: Latest US Patents, China's latest patents, Technical Efficacy Thesaurus, Application Domain, Technology Topic, Popular Technical Reports.
© 2025 PatSnap. All rights reserved.Legal|Privacy policy|Modern Slavery Act Transparency Statement|Sitemap|About US| Contact US: help@patsnap.com