Device and method for repairing layering damage of carbon fiber reinforced thermosetting resin-based composite material
A composite material and damage repair technology, which is applied in the field of composite material repair, can solve the problems of electrochemical corrosion and stress corrosion at bolt joints, failure to apply, and damage to fiber continuity, so as to restore basic mechanical properties, reduce repair costs, and retain The effect of layer performance
- Summary
- Abstract
- Description
- Claims
- Application Information
AI Technical Summary
Problems solved by technology
Method used
Image
Examples
Embodiment 1
[0088] 1. Preparation of planar plate members with delamination damage. Firstly, carbon fiber / epoxy resin composite laminates were prepared by vacuum assisted forming (VARI) process, and the fiber volume fraction of the formed components was calculated to be 80%. The selected carbon fiber is T700 grade, and its combustion and oxidation temperature is about 400°C; the selected epoxy resin is bisphenol A epoxy resin, and its combustion and carbonization temperature is above 200°C. The laminates were then subjected to low-velocity impact treatment using a drop weight impact tester. The speed not greater than the penetration energy of the test piece is selected for low-speed impact of the falling weight, so that the test piece will be damaged by interlayer delamination and epoxy resin breakage, and a flat plate member 1 with delamination damage will be obtained. During the application of the impact load, the impact contact force of the composite member is collected synchronously ...
Embodiment 2
[0094] Embodiment 2: The difference between this embodiment and Embodiment 1 is that the member prepared by the VARI process in step 1 is a curved plate member.
Embodiment 3
[0095] Embodiment 3: The difference between this embodiment and Embodiment 1 is that the member prepared by the VARI process in step 1 is a circular tubular member.
PUM
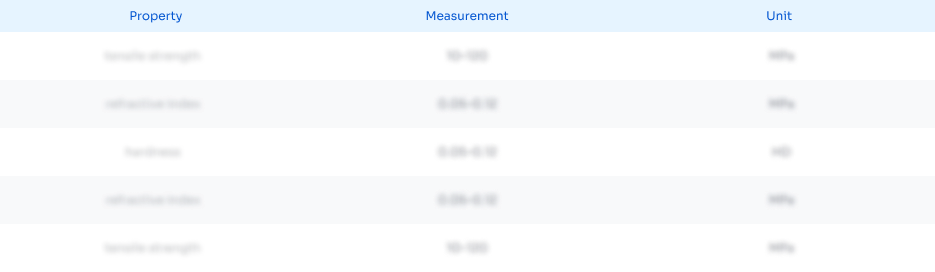
Abstract
Description
Claims
Application Information

- Generate Ideas
- Intellectual Property
- Life Sciences
- Materials
- Tech Scout
- Unparalleled Data Quality
- Higher Quality Content
- 60% Fewer Hallucinations
Browse by: Latest US Patents, China's latest patents, Technical Efficacy Thesaurus, Application Domain, Technology Topic, Popular Technical Reports.
© 2025 PatSnap. All rights reserved.Legal|Privacy policy|Modern Slavery Act Transparency Statement|Sitemap|About US| Contact US: help@patsnap.com