Low-silicon medium-carbon gear steel suitable for cold forging machining and manufacturing method thereof
A carbon gear steel and cold forging technology, applied in the field of gear steel and its manufacturing, can solve problems such as difficulty in meeting cold forging process requirements
- Summary
- Abstract
- Description
- Claims
- Application Information
AI Technical Summary
Problems solved by technology
Method used
Image
Examples
Embodiment 2
[0045] The smelting uses electric furnace + refining furnace + VD furnace to smelt 100 tons of steel with the chemical composition shown below, and uses continuous casting to make continuous casting slabs with a cross-sectional size of 300mm×340mm. The chemical composition of the obtained continuous casting slabs includes: : C: 0.41%, Si: 0.05%, Mn: 0.52%, Cr: 0.37%, P: 0.011%, S: 0.017%, Al: 0.019%, N: 0.008%, Cu: 0.02%, Ni: 0.02% , Mo: 0.01%, B: 0.0016%, Ti: 0.004%, [O]: 0.0010%, (Cu+Ni+Mo): 0.05%, and the balance is Fe and unavoidable impurity elements.
[0046] The continuous casting slab needs to be heated to 1140°C, and the slab is kept warm for 4 hours before leaving the heating furnace. The air-to-coal ratio of the heating gas is in the range of 1.01-1.07. Rolling is carried out after descaling with high-pressure water: the starting rolling temperature is 1050°C, and the final rolling The temperature is 920°C. After the final rolling, the steel is slowly cooled with a ...
PUM
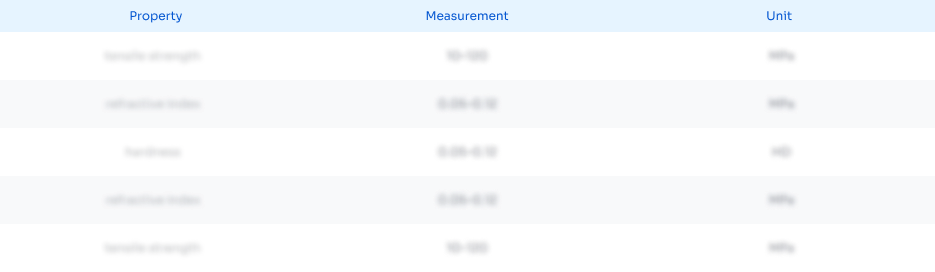
Abstract
Description
Claims
Application Information

- R&D
- Intellectual Property
- Life Sciences
- Materials
- Tech Scout
- Unparalleled Data Quality
- Higher Quality Content
- 60% Fewer Hallucinations
Browse by: Latest US Patents, China's latest patents, Technical Efficacy Thesaurus, Application Domain, Technology Topic, Popular Technical Reports.
© 2025 PatSnap. All rights reserved.Legal|Privacy policy|Modern Slavery Act Transparency Statement|Sitemap|About US| Contact US: help@patsnap.com