Method for preparing high-carbon linear alpha-olefin through hydrogenation of CO2 and application
An olefin reaction, high-carbon technology, applied in the direction of hydrocarbon production from carbon oxides, chemical instruments and methods, metal/metal oxide/metal hydroxide catalysts, etc., can solve the problems of difficult industrialization and low olefin selectivity , to achieve the effect of promoting high selectivity formation, simple preparation process, and improving carbon chain coupling ability
- Summary
- Abstract
- Description
- Claims
- Application Information
AI Technical Summary
Problems solved by technology
Method used
Image
Examples
Embodiment 1
[0025] The iron catalyst preparation process is as follows:
[0026] Dissolve 10 g of glucose and 12 g of ferric nitrate nonahydrate in 150 mL of deionized water, and stir vigorously. The resulting mixed solution was transferred to a hydrothermal synthesis reactor with a polytetrafluoroethylene liner. The autoclave was sealed and transferred to a hydrothermal synthesis facility. The condition control of the hydrothermal synthesis process is 120° C. for 20 hours. The obtained product distribution was repeatedly washed several times with deionized water and absolute ethanol. Finally, the product was dried for more than 12 hours, and it was taken out, which was recorded as Fe / C. The Fe / C of 1.2g, the potassium carbonate powder of 0.11g, the magnesium oxide powder of 0.018g, the calcium carbonate powder of 0.06g are mechanically mixed in the mode of grinding, and Fe content is 14% in the catalyzer, and the catalyst prepared is denoted as Fe / C-K-Ca-Mg.
[0027] The prepared ca...
Embodiment 2
[0029] The iron catalyst preparation process is as follows:
[0030]Dissolve 10 g of glucose and 12 g of ferric nitrate nonahydrate in 150 mL of deionized water, and stir vigorously. The resulting mixed solution was transferred to a hydrothermal synthesis reactor with a polytetrafluoroethylene liner. The autoclave was sealed and transferred to a hydrothermal synthesis facility. The condition control of the hydrothermal synthesis process is 120° C. for 20 hours. The obtained product distribution was repeatedly washed several times with deionized water and absolute ethanol. Finally, the product was dried for more than 12 hours, and it was taken out, which was recorded as Fe / C. 1.2g of Fe / C, 0.144g of potassium carbonate powder, and 0.048g of magnesium oxide powder were mechanically mixed by grinding, and the prepared catalyst was recorded as Fe / C-K-Mg. The content of Fe in the catalyst is 14%, and the prepared catalyst is recorded as Fe / C-K-Mg.
[0031] The prepared catalys...
Embodiment 3
[0033] The iron catalyst preparation process is as follows:
[0034] Dissolve 10 g of glucose and 12 g of ferric nitrate nonahydrate in 150 mL of deionized water, and stir vigorously. The resulting mixed solution was transferred to a hydrothermal synthesis reactor with a polytetrafluoroethylene liner. The autoclave was sealed and transferred to a hydrothermal synthesis facility. The condition control of the hydrothermal synthesis process is 120° C. for 20 hours. The obtained product distribution was repeatedly washed several times with deionized water and absolute ethanol. Finally, the product was dried for more than 12 hours, and it was taken out, which was recorded as Fe / C. 1.2g of Fe / C, 0.144g of potassium carbonate powder, and 0.204g of calcium carbonate powder were mechanically mixed by grinding, and the prepared catalyst was recorded as Fe / C-K-Ca-I. The content of Fe in the catalyst is 14%, and the prepared catalyst is recorded as Fe / C-K-Ca-I.
[0035] The prepared ...
PUM
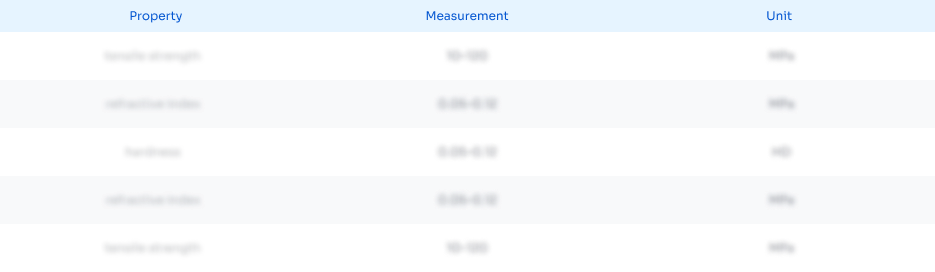
Abstract
Description
Claims
Application Information

- R&D Engineer
- R&D Manager
- IP Professional
- Industry Leading Data Capabilities
- Powerful AI technology
- Patent DNA Extraction
Browse by: Latest US Patents, China's latest patents, Technical Efficacy Thesaurus, Application Domain, Technology Topic, Popular Technical Reports.
© 2024 PatSnap. All rights reserved.Legal|Privacy policy|Modern Slavery Act Transparency Statement|Sitemap|About US| Contact US: help@patsnap.com