Corn inter-row operation robot and inter-row running control method thereof
An operation robot and robot technology, applied in the direction of control drive, agricultural machinery and tools, botanical equipment and methods, etc., can solve the problem that the left and right wheels have different subsidence and slip rates, and cannot realize the smooth straight running of the operation machinery and the driving force of the driving force. To achieve the effect of automatic line-changing operation, flexible walking and steering, and reducing course deviation
- Summary
- Abstract
- Description
- Claims
- Application Information
AI Technical Summary
Problems solved by technology
Method used
Image
Examples
Embodiment Construction
[0057] The present invention will be further described below in conjunction with the accompanying drawings to make those skilled in the art with reference to the specification.
[0058] Such as Figure 1-6 As shown, the present invention provides a corn row work robot, which mainly includes a frame 100, two screw drive wheels 200, 300, a scraper plate 400, and a liquid discharge device 500.
[0059] Such as figure 2 As shown, the frame 100 includes a carrier plate 110, two first cantilever beams 121, 122, and two second cantilever beams 131, 132. In this embodiment. The frame 100 is a rectangular plate; two first cantilever beams 121, 122 are symmetrically mounted on both sides of the carrier plate 110, close to one end of the carrier plate 110; two second cantilever beams 131, 132 are symmetrically mounted on the carrier 110 On both sides and the other end of the carrier plate 110 is disposed.
[0060] One end of the two first cantilever beams 121, 122 is fixed to the bottom of th...
PUM
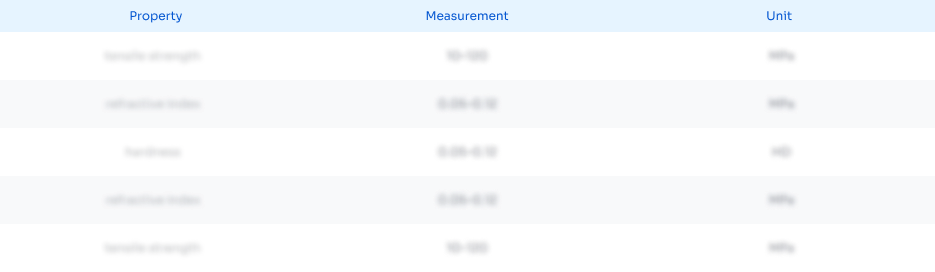
Abstract
Description
Claims
Application Information

- R&D
- Intellectual Property
- Life Sciences
- Materials
- Tech Scout
- Unparalleled Data Quality
- Higher Quality Content
- 60% Fewer Hallucinations
Browse by: Latest US Patents, China's latest patents, Technical Efficacy Thesaurus, Application Domain, Technology Topic, Popular Technical Reports.
© 2025 PatSnap. All rights reserved.Legal|Privacy policy|Modern Slavery Act Transparency Statement|Sitemap|About US| Contact US: help@patsnap.com