Heat treatment process of duplex stainless steel composite plate
A duplex stainless steel and clad plate technology, applied in heat treatment furnaces, heat treatment equipment, manufacturing tools, etc., can solve the problems of large performance loss of carbon steel structures, unfavorable product applications, etc., and achieve the effect of ensuring structural performance and corrosion resistance
- Summary
- Abstract
- Description
- Claims
- Application Information
AI Technical Summary
Problems solved by technology
Method used
Image
Examples
Embodiment 1
[0018] Step 1: Using a trolley-type heating furnace, first raise the temperature of the heating furnace to 500°C;
[0019] Step 2: Put the sample into the heating furnace, wait for the temperature to rise to 500°C, and keep it warm for 84 minutes;
[0020] Step 3: Take the sample out of the heating furnace and air cool;
[0021] The microstructure of the duplex stainless steel finally obtained in this embodiment is as follows: figure 1 As shown at 500°C, the austenite content is 46.95%, and there is no harmful second phase precipitated at the phase interface between austenite and ferrite. Pitting corrosion test, the surface is smooth and bright, no pitting pits appear, the sample passed the pitting corrosion test.
Embodiment 2
[0023] Step 1: Using a trolley-type heating furnace, first raise the temperature of the heating furnace to 520°C;
[0024] Step 2: Put the sample into the heating furnace, wait for the temperature to rise to 520°C, and keep it warm for 62 minutes;
[0025] Step 3: Take the sample out of the heating furnace and air cool;
[0026] The microstructure of the duplex stainless steel finally obtained in this embodiment is as follows: figure 1 As shown at 520°C, the austenite content is 45.93%, and there is no harmful second phase precipitated at the phase interface between austenite and ferrite. Pitting corrosion test, the surface is smooth and bright, no pitting pits appear, the sample passed the pitting corrosion test.
Embodiment 3
[0028] Step 1: Using a trolley heating furnace, first raise the temperature of the heating furnace to 540°C;
[0029] Step 2: Put the sample into the heating furnace, wait for the temperature to rise to 540 ° C, and keep it for 93 minutes;
[0030] Step 3: Take the sample out of the heating furnace and air cool;
[0031] The microstructure of the duplex stainless steel finally obtained in this embodiment is as follows: figure 1 As shown at 540°C, the austenite content is 50.60%, and there is no harmful second phase precipitated at the phase interface between austenite and ferrite. Pitting corrosion test, the surface is smooth and bright, no pitting pits appear, the sample passed the pitting corrosion test.
PUM
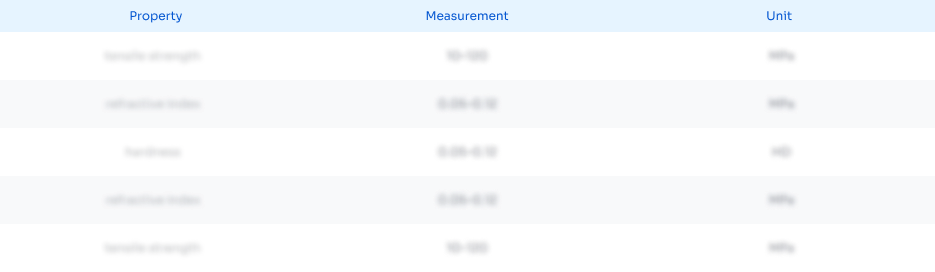
Abstract
Description
Claims
Application Information

- R&D
- Intellectual Property
- Life Sciences
- Materials
- Tech Scout
- Unparalleled Data Quality
- Higher Quality Content
- 60% Fewer Hallucinations
Browse by: Latest US Patents, China's latest patents, Technical Efficacy Thesaurus, Application Domain, Technology Topic, Popular Technical Reports.
© 2025 PatSnap. All rights reserved.Legal|Privacy policy|Modern Slavery Act Transparency Statement|Sitemap|About US| Contact US: help@patsnap.com