Austenitic stainless steel, fine-grain large-specification bar and preparation method and application of fine-grain large-specification bar
An austenitic stainless steel, large-scale technology, applied in the field of metal materials, can solve the problems of low tensile strength, unsatisfactory, easy mixed crystals, etc., to achieve the effect of satisfying long life, increasing manufacturing cost and ensuring stability
- Summary
- Abstract
- Description
- Claims
- Application Information
AI Technical Summary
Problems solved by technology
Method used
Image
Examples
Embodiment 1
[0036] 1) The electric furnace (EF+AOD+LF)+electroslag remelting smelting process was used to obtain a Φ550mm stainless steel ingot, and the chemical composition is shown in Table 1;
[0037] 2) Heating the obtained ingot to 1200±20°C, holding it for 8 hours, and performing billet forging on a 4000-ton fast forging machine to obtain a 350mm octagonal intermediate forging billet;
[0038] 3) Heat the 350mm octagonal intermediate forging billet to 1150±20°C, keep it warm for 3 hours, and forge it on a 1300-ton radial forging machine to obtain a large-size bar of Φ160mm;
[0039] 4) Heat the Φ160mm forged bar to 900±20°C, keep it warm for 3 hours, and cool it to room temperature with water to obtain a fine-grained large-scale bar;
[0040] 5) The Φ160mm forged bar was tested for mechanical properties and grain size, and the results are shown in Table 2.
Embodiment 2
[0042] 1) The smelting process of electric furnace (EF+AOD+LF) was adopted to obtain 2.3 tons of stainless steel ingots, and the chemical composition is shown in Table 1;
[0043] 2) Heating the obtained ingot to 1250±20°C, holding it for 4 hours, and performing billet forging on a 2000-ton fast forging machine to obtain a 280mm octagonal intermediate forging billet;
[0044] 3) Heat the 280mm octagonal intermediate forging billet to 1100±20°C, keep it warm for 3 hours, and roll it on the rolling mill to obtain a large-size bar with a diameter of Φ100mm;
[0045] 4) Heat the Φ100mm rolled bar to 1080±20°C, keep it warm for 0.2 hours, and air-cool to room temperature to obtain fine-grained large-scale bars;
[0046] 5) The Φ100mm forged bar was tested for mechanical properties and grain size, and the results are shown in Table 2.
Embodiment 3
[0048] 1) The electric furnace (EF+AOD+LF)+electroslag remelting smelting process was used to obtain a Φ510mm stainless steel ingot, and the chemical composition is shown in Table 1;
[0049] 2) Heating the obtained ingot to 1250±20°C, holding it for 4 hours, and performing billet forging on a 2000-ton fast forging machine to obtain a 250mm octagonal intermediate forging billet;
[0050] 3) Heat the 250mm octagonal intermediate forging billet to 1050±20°C, keep it warm for 3 hours, and forge it on a 1300-ton diameter forging machine to obtain a large-sized bar with a diameter of Φ130mm;
[0051] 4) Heat the Φ130mm forged bar to 1000±20°C, keep it warm for 0.2 hours, and cool it to room temperature with water to obtain a fine-grained large-scale bar;
[0052] 5) The Φ130mm forged bar was tested for mechanical properties and grain size, and the results are shown in Table 2.
[0053] Chemical composition (mass percentage) of austenitic stainless steel in table 1 embodiment of th...
PUM
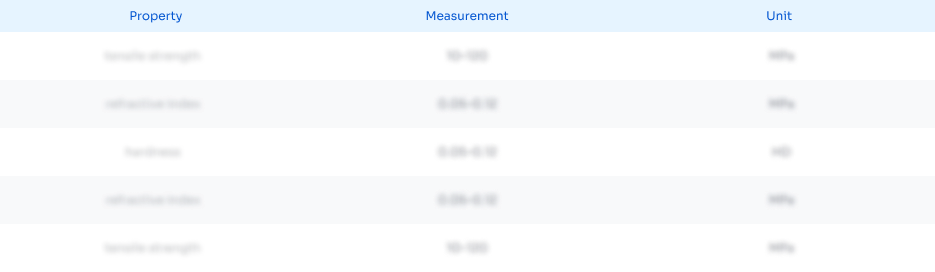
Abstract
Description
Claims
Application Information

- R&D
- Intellectual Property
- Life Sciences
- Materials
- Tech Scout
- Unparalleled Data Quality
- Higher Quality Content
- 60% Fewer Hallucinations
Browse by: Latest US Patents, China's latest patents, Technical Efficacy Thesaurus, Application Domain, Technology Topic, Popular Technical Reports.
© 2025 PatSnap. All rights reserved.Legal|Privacy policy|Modern Slavery Act Transparency Statement|Sitemap|About US| Contact US: help@patsnap.com