Process for synthesizing methyl methacrylate from ethanol
A technology of methyl methacrylate and methyl propionate, which is applied in the field of synthesis of methyl methacrylate, can solve problems affecting economic and social stability, achieve the effects of increasing economic added value, broadening the downstream product chain of coal, and reducing the impact
- Summary
- Abstract
- Description
- Claims
- Application Information
AI Technical Summary
Problems solved by technology
Method used
Image
Examples
Embodiment 1
[0031] The technical process of present embodiment ethanol synthetic methyl methacrylate is as figure 1 As shown, the specific process is as follows:
[0032] Raw material ethanol and CO enter the oxo synthesis reaction kettle a that catalyst (catalyst uses rhodium as active component, ethyl iodide as auxiliary agent, and lithium iodide as stabilizer) is housed through pipeline 1 and pipeline 2 respectively, and the reaction temperature is 150 ℃, pressure 2.5MPa. The propionic acid selectivity is greater than 90%, and the space-time yield is greater than 2.0mol / L / h. The still liquid containing propionic acid enters the flash tank b through pipeline 6, and the pressure drops to 0.15MPa. The partially vaporized liquid and CO enter the propionic acid separation tower c through the pipeline 4, and the unvaporized liquid, including propionic acid, unreacted ethanol, rhodium catalyst and other components, returns to the oxo reactor a through the pipeline 5 to continue to participa...
Embodiment 2
[0036] The reaction temperature in the oxo synthesis propionic acid operation in embodiment 1 becomes 200 ℃, and reaction pressure becomes 3.5MPa, and catalyzer becomes catalyzer (catalyst is active component with iridium, iodoethane is auxiliary agent, formylmorpholine is a stabilizer), the propionic acid selectivity is greater than 95%, and the space-time yield is greater than 2.8mol / L / h. The reactor in the esterification process is changed into a fixed-bed adiabatic reactor, the reaction temperature is 130° C., the reaction pressure is 0.3 MPa, and the catalyst is a sulfonic acid resin. The selectivity of methyl propionate is greater than 97%, and the conversion rate of methanol is greater than 98%. The temperature of the reactor in the aldol condensation reaction step is changed to 440° C., the pressure is changed to 0.3 MPa, the selectivity of methyl methacrylate is greater than 92%, and the conversion rate of formaldehyde is greater than 80%.
PUM
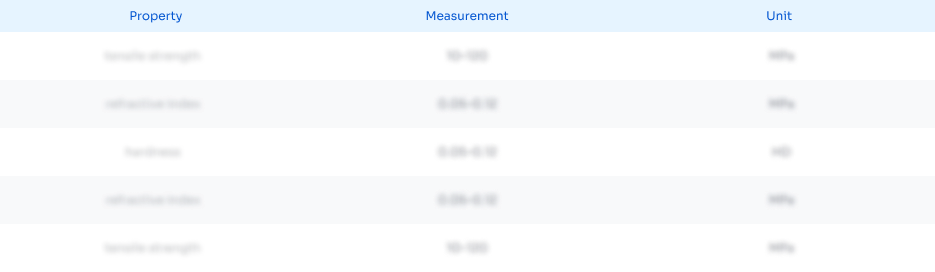
Abstract
Description
Claims
Application Information

- Generate Ideas
- Intellectual Property
- Life Sciences
- Materials
- Tech Scout
- Unparalleled Data Quality
- Higher Quality Content
- 60% Fewer Hallucinations
Browse by: Latest US Patents, China's latest patents, Technical Efficacy Thesaurus, Application Domain, Technology Topic, Popular Technical Reports.
© 2025 PatSnap. All rights reserved.Legal|Privacy policy|Modern Slavery Act Transparency Statement|Sitemap|About US| Contact US: help@patsnap.com