Multi-solvent system lithium ion battery negative electrode proportioning method
A lithium-ion battery and multi-solvent technology, applied in battery electrodes, electrode manufacturing, secondary batteries, etc., can solve the problems of thickener agglomeration, uneven powder mixing, etc., and achieve improved cracking, good density consistency, and appearance good effect
- Summary
- Abstract
- Description
- Claims
- Application Information
AI Technical Summary
Problems solved by technology
Method used
Examples
Embodiment 1
[0029] 1. Put the negative electrode active material, conductive agent, thickener and other powders into the mixing tank according to the mass ratio (active material: conductive agent: thickener = 95: 1.5: 1.5), then start stirring for 45 minutes, stirring revolution 20rpm , rotation 500rpm, mixing powder;
[0030] 2. Add 70% of the deionized water with a mass ratio of 100 into the mixing tank, first turn on the low-speed stirring for 45 minutes, stir the revolution at 20 rpm, and rotate at 500 rpm;
[0031] 3. Add the remaining 30% deionized water, start the rapid stirring, the time is 90min, the revolution is 30rpm, and the rotation is 1500rpm;
[0032] 4. Add the binder with a mass ratio of 2, start the rapid stirring, the time is 30min, the revolution is 30rpm, and the rotation is 1500rpm;
[0033] 5. Add a modifier with a mass ratio of 3, start rapid stirring for 30 minutes, revolution at 30 rpm, and rotation at 1200 rpm.
Embodiment 2
[0035] 1. Put the negative electrode active material, conductive agent, thickener and other powders into the mixing tank according to the mass ratio (active material: conductive agent: thickener = 96: 1.2: 1.5), then start stirring for 45 minutes, stirring revolution 20rpm , rotation 500rpm, mixing powder;
[0036] 2. Add 70% of the deionized water with a mass ratio of 90 to the mixing tank, first turn on the low-speed stirring for 45 minutes, stir at 20 rpm, and rotate at 500 rpm;
[0037] 3. Add the remaining 30% deionized water and a modifier with a mass ratio of 6, start rapid stirring for 120 minutes, revolution at 30 rpm, and rotation at 1500 rpm;
[0038] 4. Add a binder with a mass ratio of 1.3, start rapid stirring for 30 minutes, revolution at 30rpm, and rotation at 1500rpm.
Embodiment 3
[0040] 1. Put the negative electrode active material, conductive agent, thickener and other powder materials into the mixing tank according to the mass ratio (active material: conductive agent: thickener = 96.5: 0.5: 1.7), then start stirring for 45 minutes, stirring revolution 20rpm , rotation 500rpm, mixing powder;
[0041] 2. Add 70% of the deionized water with a mass ratio of 105 into the mixing tank, first turn on the low-speed stirring for 45 minutes, stir the revolution at 20 rpm, and rotate at 500 rpm;
[0042] 3. Add the remaining 30% deionized water and turn it on quickly
[0043] Stirring time 90min, revolution 30rpm, rotation 1500rpm;
[0044] 4. Add a binder with a mass ratio of 1.3 and a modifier with a mass ratio of 6, start rapid stirring for 30 minutes, revolution at 30 rpm, and rotation at 1500 rpm.
[0045] The experimental data of present embodiment 1-3 is shown in the table below:
[0046] Numbering Slurry viscosity / cP Fineness / μm settlem...
PUM
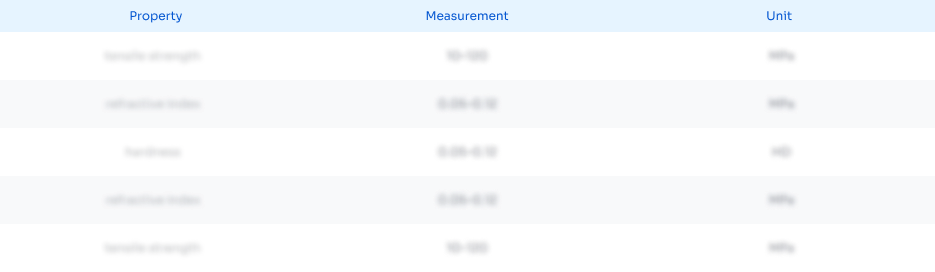
Abstract
Description
Claims
Application Information

- R&D
- Intellectual Property
- Life Sciences
- Materials
- Tech Scout
- Unparalleled Data Quality
- Higher Quality Content
- 60% Fewer Hallucinations
Browse by: Latest US Patents, China's latest patents, Technical Efficacy Thesaurus, Application Domain, Technology Topic, Popular Technical Reports.
© 2025 PatSnap. All rights reserved.Legal|Privacy policy|Modern Slavery Act Transparency Statement|Sitemap|About US| Contact US: help@patsnap.com