Tapered roller bearing retainer automatic positioning mechanism and control method thereof
A tapered roller bearing, automatic positioning technology, applied in the direction of shafts and bearings, bearing components, positioning devices, etc., can solve problems such as offset, easily damaged molds, and no mold protection function, so as to improve product quality and maintain stability Effect
- Summary
- Abstract
- Description
- Claims
- Application Information
AI Technical Summary
Problems solved by technology
Method used
Image
Examples
Embodiment Construction
[0031] The specific implementation manners of the present invention will be further described in detail below in conjunction with the accompanying drawings and embodiments. The following examples are used to illustrate the present invention, but are not intended to limit the scope of the present invention.
[0032] Such as Figure 1 to Figure 4 As shown, the automatic positioning mechanism of the tapered roller bearing cage of the present invention, it has been explained in advance that the tapered roller bearing cage 1 is the product to be positioned, and it is umbrella-shaped as a whole, and has regularly distributed ribs 2, Adjacent ribs 2 see hollowed-out windows 3 .
[0033] This mechanism includes servo transfer mechanism 100, slide rail 200, lifting mechanism 300, gripper mechanism 400, product positioning mechanism 500 and lower mold 600, wherein, lifting mechanism 300 is fixedly connected with servo transfer mechanism 100, and servo transfer mechanism 100 drives The...
PUM
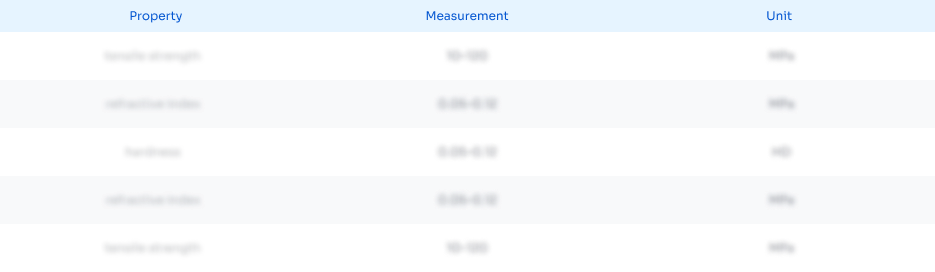
Abstract
Description
Claims
Application Information

- R&D
- Intellectual Property
- Life Sciences
- Materials
- Tech Scout
- Unparalleled Data Quality
- Higher Quality Content
- 60% Fewer Hallucinations
Browse by: Latest US Patents, China's latest patents, Technical Efficacy Thesaurus, Application Domain, Technology Topic, Popular Technical Reports.
© 2025 PatSnap. All rights reserved.Legal|Privacy policy|Modern Slavery Act Transparency Statement|Sitemap|About US| Contact US: help@patsnap.com