Display device
A technology for a display device and a display panel, applied in the field of backlight, can solve the problems of inability to be tightly fixed, high bonding reliability and bonding strength, poor compatibility between plastic frames and cast aluminum parts, etc., so as to meet the needs of narrow borders and improve cooperation stability. the effect of reducing the thickness of the border
- Summary
- Abstract
- Description
- Claims
- Application Information
AI Technical Summary
Problems solved by technology
Method used
Image
Examples
Embodiment
[0033] Such as figure 1 As shown, in this embodiment, the display device of the present invention includes an outer frame 100 , a sheet metal part 200 , a light guide plate 300 , a film layer 400 , an adhesive layer 500 , a display panel 600 and a cover plate 700 .
[0034] Such as figure 2 As shown, the outer frame 100 is a die-casting part, and its material is copper, zinc, aluminum or aluminum alloy. The outer frame 100 is a box body with a concave center, the box body includes a bottom plate 110 and side plates 120 surrounding the bottom plate 110, the bottom plate 110 is a rectangular plate, and the side plates 120 surround the rectangular plate. On the outer edge of the plate, one side of the bottom plate 110 is provided with two grooves 111, and the openings of the grooves 111 are arranged inside the box body, specifically, the grooves 111 are elongated grooves , are provided at the two shorter edges of the rectangular plate, and one side surface of the groove 111 is...
PUM
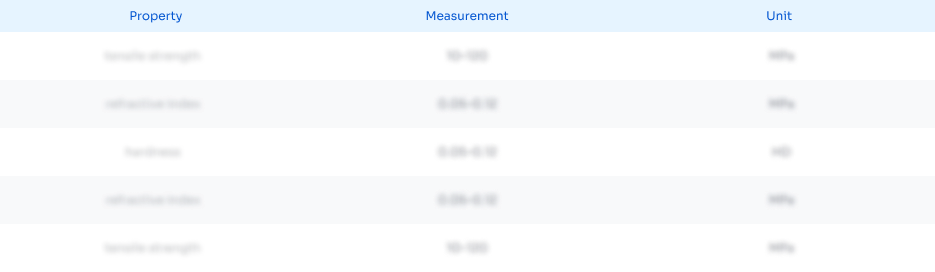
Abstract
Description
Claims
Application Information

- Generate Ideas
- Intellectual Property
- Life Sciences
- Materials
- Tech Scout
- Unparalleled Data Quality
- Higher Quality Content
- 60% Fewer Hallucinations
Browse by: Latest US Patents, China's latest patents, Technical Efficacy Thesaurus, Application Domain, Technology Topic, Popular Technical Reports.
© 2025 PatSnap. All rights reserved.Legal|Privacy policy|Modern Slavery Act Transparency Statement|Sitemap|About US| Contact US: help@patsnap.com