Novel hard alloy inner-cooling deep hole twist drill
A cemented carbide and twist drill technology, which is applied in twist drills, drilling/drilling equipment, drill repairing, etc., can solve the problems that chips cannot be taken away quickly, broken, easy to generate vibration, etc.
- Summary
- Abstract
- Description
- Claims
- Application Information
AI Technical Summary
Problems solved by technology
Method used
Image
Examples
Embodiment Construction
[0032] The embodiments of the present invention are described in detail below, so that the advantages and features of the present invention can be more easily understood by those skilled in the art, so as to define the protection scope of the present invention more clearly.
[0033] like Figure 1-6 As shown, a new hard alloy internal cooling deep hole twist drill includes a cylindrical handle 1 and a cutter body arranged on the cylindrical handle 1. The cutter body includes a cutting edge 2 and is used to connect the cylindrical handle 1 and the The transition neck 3 of the cutting edge 2; the material of the cutter body is 10% cobalt, and the fracture toughness is K IC Higher submicron carbide internally cooled bar stock; diameter d of cylindrical shank 1 1 Greater than or equal to the diameter d of the cutting edge portion 2 2 The minimum even value of the cutting edge part 2 diameter d 2 3mm to 10mm.
[0034] like figure 2 As shown, due to the long overhang of the de...
PUM
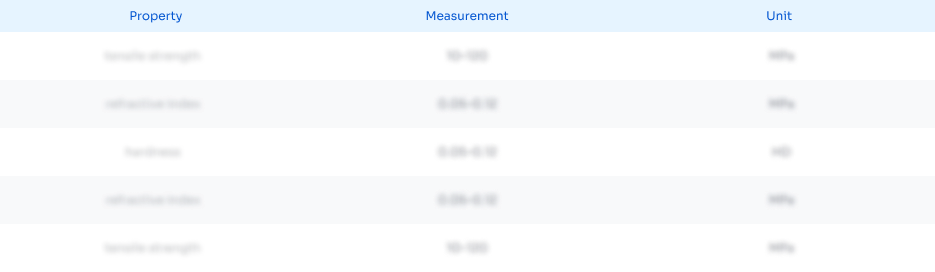
Abstract
Description
Claims
Application Information

- R&D
- Intellectual Property
- Life Sciences
- Materials
- Tech Scout
- Unparalleled Data Quality
- Higher Quality Content
- 60% Fewer Hallucinations
Browse by: Latest US Patents, China's latest patents, Technical Efficacy Thesaurus, Application Domain, Technology Topic, Popular Technical Reports.
© 2025 PatSnap. All rights reserved.Legal|Privacy policy|Modern Slavery Act Transparency Statement|Sitemap|About US| Contact US: help@patsnap.com