Self-centering anti-vibration clamp for gear grinding machining of thin radial plate gear part and clamping method
A self-centering and spoke technology, applied in gear tooth manufacturing devices, manufacturing tools, components with teeth, etc., can solve the problem of failure to meet design requirements, difficulty in clamping and aligning parts, and affecting the safety and use of parts. life and other issues, to achieve the effect of improving the processing quality
- Summary
- Abstract
- Description
- Claims
- Application Information
AI Technical Summary
Problems solved by technology
Method used
Image
Examples
Embodiment 1
[0035] Such as Figures 1 to 10 As shown, a self-centering anti-vibration fixture for the grinding of thin-web gear parts according to the present invention includes a mandrel 1, a tapered sleeve 4 and a nut 5, and the mandrel 1 includes spherical columns 11 from bottom to top , Conical frustum 12, center column 13 and external thread 14, nut 5 is matched with external thread 14, taper sleeve 4 is set outside the center column 13; thin spoke plate gear part 7 includes through-hole shaft 71 and circumferentially arranged on the through-hole The thin-walled radial plate 72 on the outer wall of the hole shaft 71, the inner hole of the through hole shaft 71 passes through the center column 13 and the lower end of the inner hole is matched with the cone 12; the taper sleeve 4 is located between the through hole shaft 71 and the nut 5 and the lower end of the taper sleeve 4 Cooperate with the upper end of the inner hole of the through-hole shaft 71, tighten the nut 5 to fix the thro...
PUM
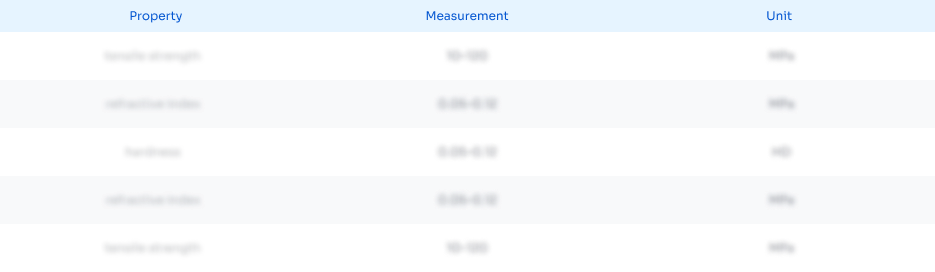
Abstract
Description
Claims
Application Information

- Generate Ideas
- Intellectual Property
- Life Sciences
- Materials
- Tech Scout
- Unparalleled Data Quality
- Higher Quality Content
- 60% Fewer Hallucinations
Browse by: Latest US Patents, China's latest patents, Technical Efficacy Thesaurus, Application Domain, Technology Topic, Popular Technical Reports.
© 2025 PatSnap. All rights reserved.Legal|Privacy policy|Modern Slavery Act Transparency Statement|Sitemap|About US| Contact US: help@patsnap.com