Middle assembling robot welding process for ship
A technology of robot welding and welding technology, applied in welding equipment, welding accessories, manufacturing tools, etc., can solve the problems that robot welding technology cannot meet flexible and diverse welding requirements, complex welding paths, and irregular structural forms of components, etc., to achieve High commercial promotion value, stable and reliable welding quality, and the effect of improving weld quality
- Summary
- Abstract
- Description
- Claims
- Application Information
AI Technical Summary
Problems solved by technology
Method used
Image
Examples
Embodiment 1
[0029] The present invention adopts a large-span semi-gantry gantry structure, cooperates with the external axis of the robot that can move back and forth, left and right, and up and down, and the automatic visual positioning technology to quickly realize the positioning of the welding seam. The positioning technology here is the existing technology, and it will not be discussed here How to realize the welding seam positioning is described in detail. The welding robot and welding torch used are also existing technologies. The welding adopts solid wire mixed gas shielded welding (GMAW), and arc tracking is used in the welding process. In conjunction with the use, it is used to weld the flat angle and vertical angle welds of the vertical components in the ship. After the welding has been performed for a certain period of time, the welding torch will be cleaned, cut wire, and sprayed with oil until all welds are welded.
[0030] Specific steps are as follows:
[0031] a) The rob...
Embodiment 2
[0041] The robot welding system mainly consists of a large-span semi-gantry robot welding gantry system, a robot welding system, a 3D laser scanning system, and a point laser positioning system. The 3D scanning system generates discrete point cloud data by scanning the key nodes of the workpiece. The point cloud data is analyzed, calculated and redeveloped to generate the outline and coordinate data of the key nodes of the workpiece; the point laser replaces the traditional contact positioning through the precise distance measurement of the visual sensing system, which greatly improves the flexibility and efficiency of positioning.
[0042] a) Preparation before welding: After the workpiece is moved in place, the assembly accuracy of the workpiece and the specification and size of the tacking welding shall be manually inspected. The maximum assembly gap of the fillet weld shall be 3mm, the height of the tacking welding foot shall be ≤5mm, and the two ends of the tacking welding ...
PUM
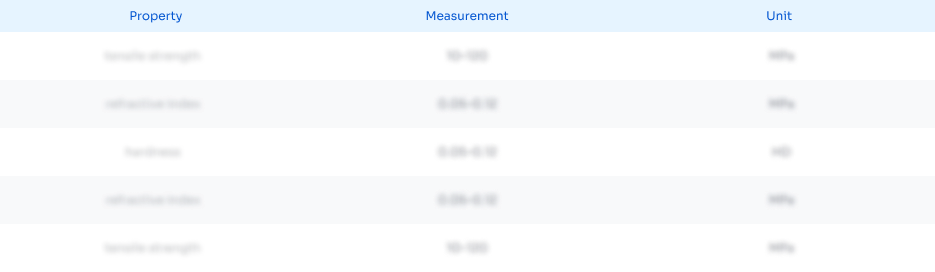
Abstract
Description
Claims
Application Information

- R&D
- Intellectual Property
- Life Sciences
- Materials
- Tech Scout
- Unparalleled Data Quality
- Higher Quality Content
- 60% Fewer Hallucinations
Browse by: Latest US Patents, China's latest patents, Technical Efficacy Thesaurus, Application Domain, Technology Topic, Popular Technical Reports.
© 2025 PatSnap. All rights reserved.Legal|Privacy policy|Modern Slavery Act Transparency Statement|Sitemap|About US| Contact US: help@patsnap.com