Ex-situ prevulcanization method for hydrogenation catalyst
A technology for pre-sulfiding and hydrogenating catalysts outside the vessel, which is applied in chemical instruments and methods, catalyst activation/preparation, physical/chemical process catalysts, etc., to achieve the effects of good sulfidation, high catalyst activity, and improved safety.
- Summary
- Abstract
- Description
- Claims
- Application Information
AI Technical Summary
Problems solved by technology
Method used
Examples
Embodiment 1
[0040] For the diesel hydrogenation catalyst FHUDS-8 (catalyst dosage: 100g) in the oxidation state listed in Table 1, presulfurization was carried out outside the equipment.
[0041] (1) Vulcanizing agent (elemental sulfur, the amount used is 102% of the theoretical sulfur demand of the diesel hydrogenation catalyst in oxidation state), vulcanization aid (the weight ratio of industrial soybean oil shown in Table 2 and kerosene shown in Table 4 2:1 mixture, the amount used is 25% of the weight of the oxidized diesel hydrogenation catalyst FHUDS-8) and mixed evenly to obtain the pre-sulfurized raw material; the pre-sulfurized raw material is mixed evenly with the oxidized diesel hydrogenation catalyst;
[0042] (2) heat-treat the mixed material in step (1) at 140°C for 1 hour;
[0043] (3) Lower the temperature of the mixed material in step (2) to 60°C, then add a mixture of 1.9g of phosphoric acid (1.9% of the weight of the oxidized diesel hydrogenation catalyst FHUDS-8) and 3...
Embodiment 2
[0047] For the diesel hydrogenation catalyst FHUDS-8 (catalyst dosage: 100g) in the oxidation state listed in Table 1, presulfurization was carried out outside the equipment.
[0048] (1) Vulcanizing agent (elemental sulfur, the dosage is 115% of the theoretical sulfur requirement of diesel hydrogenation catalyst in oxidized state), vulcanization aid (a mixture of industrial rapeseed oil and diesel oil at a weight ratio of 0.5:2, the dosage is oxidized 9% by weight of diesel hydrogenation catalyst FHUDS-8 in state) and mix uniformly to obtain presulfurized raw material; presulfurized raw material is mixed uniformly with oxidized diesel hydrogenation catalyst;
[0049] (2) heat-treat the mixed material in step (1) at 235°C for 1.5h;
[0050] (3) Reduce the temperature of the mixed material in step (2) to 60°C, then add 15 g of diammonium hydrogen phosphate (the amount is 15% of the weight of the diesel hydrogenation catalyst FHUDS-8 in an oxidized state), and mix well;
[0051...
Embodiment 3
[0054] The diesel hydrogenation catalyst FHUDS-8 in the oxidized state in Table 1 was presulfided outside the device (catalyst dosage 100g);
[0055] (1) Add vulcanizing agent (elemental sulfur, the amount is 90% of the theoretical sulfur requirement of diesel hydrogenation catalyst), vulcanization aid (a mixture of industrial soybean oil and white oil at a weight ratio of 2:1, and the amount is oxidized diesel oil) Hydrogen catalyst FHUDS-8 weight 25%) mixed uniformly to obtain presulfurized raw material; presulfurized raw material and oxidized diesel hydrogenation catalyst mixed uniformly;
[0056] (2) heat-treat the mixed material in step (1) at 180°C for 3.5 hours;
[0057] (3) Reduce the temperature of the mixed material in step (2) to 60°C, then add 0.5g of ammonium phosphate (the amount is 0.5% of the weight of the diesel hydrogenation catalyst FHUDS-8 in an oxidized state), and mix well;
[0058] (4) Treat the material obtained in step (3) in a hydrogen atmosphere at ...
PUM
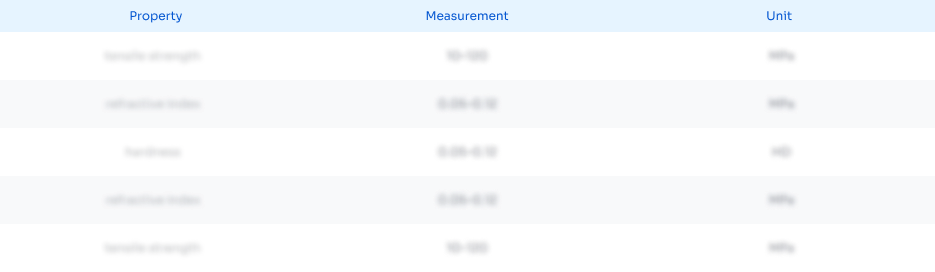
Abstract
Description
Claims
Application Information

- R&D
- Intellectual Property
- Life Sciences
- Materials
- Tech Scout
- Unparalleled Data Quality
- Higher Quality Content
- 60% Fewer Hallucinations
Browse by: Latest US Patents, China's latest patents, Technical Efficacy Thesaurus, Application Domain, Technology Topic, Popular Technical Reports.
© 2025 PatSnap. All rights reserved.Legal|Privacy policy|Modern Slavery Act Transparency Statement|Sitemap|About US| Contact US: help@patsnap.com