Flue gas desulfurization absorption system and process
An absorption system and flue gas technology, applied in the field of desulfurization, can solve the problems of lowering temperature, reducing energy consumption for analysis, and high concentration of sulfur dioxide emission at the flue gas outlet
- Summary
- Abstract
- Description
- Claims
- Application Information
AI Technical Summary
Problems solved by technology
Method used
Image
Examples
Embodiment 1
[0065] The sintering flue gas of an iron and steel enterprise, the flue gas volume is 50×10 4 m 3 / h, flue gas inlet SO 2 The concentration is 5200mg / m 3 , the flue gas temperature is 120°C, and the dust content is 20mg / m 3 , the flue gas humidity is 8%, the flue gas temperature after the flue gas is washed by washing water is 49°C, the temperature of the desulfurizer entering the desulfurization tower is 47°C, and the circulation volume of the desulfurizer is 252m 3 / h of flue gas desulfurizer reverse contact reaction, after reacting with flue gas desulfurizer, the flue gas temperature is 55°C, the opening degree of the flue gas rotating acceleration device is 60%, the flue gas velocity is 7m / s, and the flue gas enters the flue gas cooling The flue gas humidity in the section is 13.8%, and the flue gas desulfurizer content in the flue gas humidity is 0.002%. After the flue gas is cooled by the flue gas cooling section, the flue gas temperature is 46°C, and the flue gas hum...
Embodiment 2
[0067] The sintering flue gas of an iron and steel enterprise, the flue gas volume is 50×10 4 m 3 / h, flue gas inlet SO 2 The concentration is 5200mg / m 3 , the flue gas temperature is 120°C, and the dust content is 20mg / m 3 , the flue gas humidity is 10.5%, the flue gas temperature after the flue gas is washed with washing water is 49°C, the temperature of the desulfurizer entering the desulfurization tower is 47°C, and the circulation volume of the desulfurizer is 252m 3 / h flue gas desulfurizer reverse contact reaction, after reacting with flue gas desulfurizer, the flue gas temperature is 55°C, the flue gas rotation acceleration device opening is 50%, the flue gas velocity is 8m / s, and the flue gas enters the flue gas cooling The flue gas humidity in the section is 13.8%, and the flue gas desulfurizer content in the flue gas humidity is 0.001%. After the flue gas is cooled by the flue gas cooling section, the flue gas temperature is 46°C, and the flue gas humidity is 8.4...
Embodiment 3
[0069] The sintering flue gas of an iron and steel enterprise, the flue gas volume is 50×10 4 m 3 / h, flue gas inlet SO 2 The concentration is 5200mg / m 3 , the flue gas temperature is 120°C, and the dust content is 20mg / m 3, the flue gas humidity is 10.5%, the flue gas temperature after the flue gas is washed by washing water is 49°C, the temperature of the desulfurizer entering the desulfurization tower is 47°C, and the circulation volume of the desulfurizer is 252m 3 / h flue gas desulfurizer reverse contact reaction, after reacting with flue gas desulfurizer, the temperature of the flue gas is 55°C, the opening of the flue gas rotating acceleration device is 85%, the speed of the flue gas is 5m / s, and the flue gas enters the flue gas cooling The flue gas humidity in the section is 13.8%, and the flue gas desulfurizer content in the flue gas humidity is 0.021%. After the flue gas is cooled by the flue gas cooling section, the flue gas temperature is 46°C, and the flue gas ...
PUM
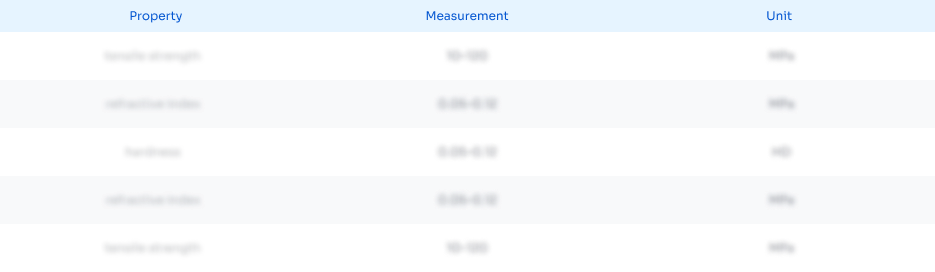
Abstract
Description
Claims
Application Information

- R&D
- Intellectual Property
- Life Sciences
- Materials
- Tech Scout
- Unparalleled Data Quality
- Higher Quality Content
- 60% Fewer Hallucinations
Browse by: Latest US Patents, China's latest patents, Technical Efficacy Thesaurus, Application Domain, Technology Topic, Popular Technical Reports.
© 2025 PatSnap. All rights reserved.Legal|Privacy policy|Modern Slavery Act Transparency Statement|Sitemap|About US| Contact US: help@patsnap.com