Purification method of sucralose-6-ethyl ester
A technology of sucralose and purification method, which is applied in the direction of organic chemical methods, chemical instruments and methods, esterified saccharides, etc., and can solve the problems of poor crystallization efficiency of ethyl acetate, large amount of organic solvent used, and large solvent consumption, etc. problems, achieve the effect of reducing the number of crystallization times and the amount of organic solvent used, high single-pass crystallization yield and efficiency, and high product yield
- Summary
- Abstract
- Description
- Claims
- Application Information
AI Technical Summary
Problems solved by technology
Method used
Image
Examples
Embodiment 1
[0053] Add 1m into the first crystallization reactor E-1 3 , Ethyl acetate (purity greater than 99%, commercially available) high-temperature saturated solution of crude sucralose-6-ethyl ester at 60°C (the crude product of sucralose-6-ethyl ester obtained in the sucralose production process is dissolved in It is prepared from ethyl acetate solvent, its purity is detected by high performance liquid chromatography), the stirring rate is 10r / min, the temperature is lowered to 40°C, 50L of n-pentane (purity greater than 99%, commercially available) is added dropwise, and Add time for 5min, continue to stir and crystallize for 0.5h. After the crystallization is completed, the material is input into the first solid-liquid separator H-1 for separation, and the separated mother liquor enters the second crystallization reactor E-2, the temperature is lowered to 30°C, the stirring rate is 10r / min, and 100L of n-pentane is added dropwise , Dropping time 10min, continue to stir and crys...
Embodiment 2
[0058] Add 2m to the first crystallization reactor E-1 3 , ethyl acetate (purity greater than 99%, commercially available) high-temperature saturated solution of crude sucralose-6-ethyl ester at 70°C (the crude product of sucralose-6-ethyl ester obtained in the sucralose production process is dissolved in It is prepared from ethyl acetate solvent, and its purity is detected by high performance liquid chromatography), the stirring rate is 20r / min, the temperature is lowered to 50°C, 200L cyclopentane is added dropwise, the dropwise addition time is 20min, and the stirring and crystallization is continued for 40min; After the crystallization is completed, the material is input into the first solid-liquid separator H-1 for separation, and the separated mother liquor enters the second crystallization reactor E-2, the temperature is lowered to 20°C, the stirring rate is 15r / min, and 150L cyclopentane is added dropwise. Add dropwise for 15 minutes, continue to stir and crystallize f...
Embodiment 3
[0063] Add 1.5m to the first crystallization reactor E-1 3 , ethyl acetate (purity greater than 99%, commercially available) high-temperature saturated solution of crude sucralose-6-ethyl ester at 65°C (the crude product of sucralose-6-ethyl ester obtained in the sucralose production process is dissolved in It is prepared from ethyl acetate solvent, its purity is detected by high performance liquid chromatography), the stirring rate is 15r / min, the temperature is lowered to 45°C, 225L of n-hexane (purity greater than 99%, commercially available) is added dropwise, and The time is 20 minutes, continue to stir and crystallize for 45 minutes; after the crystallization is completed, the material is input into the first solid-liquid separator H-1 for separation, and the separated mother liquor enters the second crystallization reactor E-2, and the temperature is lowered to 25°C, and the stirring rate is 20r / min , add 80L of n-pentane dropwise, dropwise for 10min, continue to stir a...
PUM
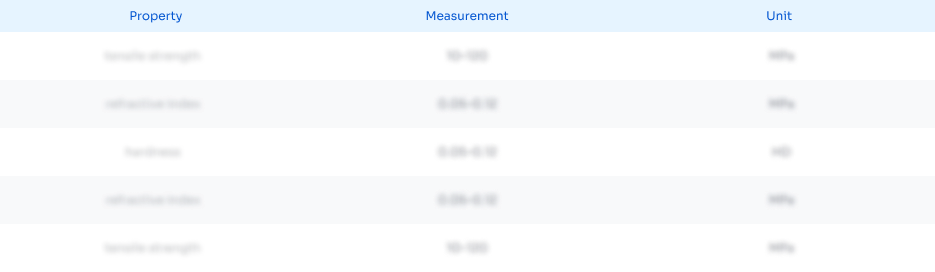
Abstract
Description
Claims
Application Information

- R&D Engineer
- R&D Manager
- IP Professional
- Industry Leading Data Capabilities
- Powerful AI technology
- Patent DNA Extraction
Browse by: Latest US Patents, China's latest patents, Technical Efficacy Thesaurus, Application Domain, Technology Topic, Popular Technical Reports.
© 2024 PatSnap. All rights reserved.Legal|Privacy policy|Modern Slavery Act Transparency Statement|Sitemap|About US| Contact US: help@patsnap.com