Anti-cracking rubber outsole
A technology of anti-cracking and rubber, which is applied in the direction of shoe soles, clothing, footwear, etc., and can solve problems such as easy cracking and insufficient elasticity of rubber outsoles
- Summary
- Abstract
- Description
- Claims
- Application Information
AI Technical Summary
Problems solved by technology
Method used
Examples
Embodiment 1
[0021] An anti-cracking rubber outsole with polyamide fiber material mixed in the rubber outsole.
[0022] The weight part of the polyamide fiber is 25, and the length is 6 mm.
[0023] The raw material of the rubber outsole includes two parts, the first part is prepared from the following raw materials in parts by weight: natural rubber (NR) 32, butadiene rubber 16.5, solution polystyrene butadiene rubber (SSBR) 17, zinc oxide 3.5 , octadecanoic acid 1.42, N-isopropyl-N`-phenyl-p-phenylenediamine 0.7, 2,2,4-trimethyl-1,2-dihydroquinoline 0.6, reinforcing agent 12.2, stop Slip agent 3.4, silane coupling agent 1.95, polyethylene glycol 1.7, the second part is the addition amount per kilogram of the first part, which is sulfur 15g, accelerator (DM) 6g, accelerator (CZ) 8g, Accelerator (D) 2g.
[0024] A preparation method of an anti-cracking rubber outsole, the specific steps are as follows:
[0025] (1) Pour the raw materials of the rubber outsole into the internal mixer for...
Embodiment 2
[0032] An anti-cracking rubber outsole with polyamide fiber material mixed in the rubber outsole.
[0033] The weight part of the polyamide fiber is 28, and the length is 5mm.
[0034] The raw material of the rubber outsole includes two parts, the first part is prepared from the following raw materials in parts by weight: natural rubber (NR) 21, butadiene rubber 32, zinc oxide 2.7, octadecanoic acid 1.6, N-iso Propyl-N`-phenyl-p-phenylenediamine 0.6, 2,2,4-trimethyl-1,2-dihydroquinoline 0.65, reinforcing agent 22.3, carbon nanotube 7.12, softener 10.3, the second Part is the amount added on a per kilogram basis for the first part, which is sulfur 12g, accelerator (DM) 7g, accelerator (CZ) 8g, accelerator (TMTD) 3g.
[0035] A preparation method of an anti-cracking rubber outsole, the specific steps are as follows:
[0036] (1) Pour the raw materials of the rubber outsole into the internal mixer for internal mixing, the time is 2 minutes, and the temperature is 130°C;
[003...
Embodiment 3
[0043] An anti-cracking rubber outsole with polyamide fiber material mixed in the rubber outsole.
[0044] The weight part of the polyamide fiber is 30, and the length is 3mm.
[0045] The raw material of the rubber outsole includes two parts, the first part is prepared from the following raw materials in parts by weight: natural rubber (NR) 13.5, butadiene rubber 50.1, zinc oxide 3.2, octadecanoic acid 1.12, N-iso Propyl-N`-phenyl-p-phenylenediamine 0.5, 2,2,4-trimethyl-1,2-dihydroquinoline 1.1, hollow glass microspheres 15.9, carbon nanotubes 7.0, reinforcing agent 4.0, Softener 5.0, the second part is the addition amount per kilogram of the first part, which is sulfur 13g, accelerator (DM) 8g, accelerator (CZ) 7g, accelerator (TMTD) 2g.
[0046] A preparation method of an anti-cracking rubber outsole, the specific steps are as follows:
[0047] (1) Pour the raw materials of the rubber outsole into the internal mixer for internal mixing, the time is 3 minutes, and the temp...
PUM
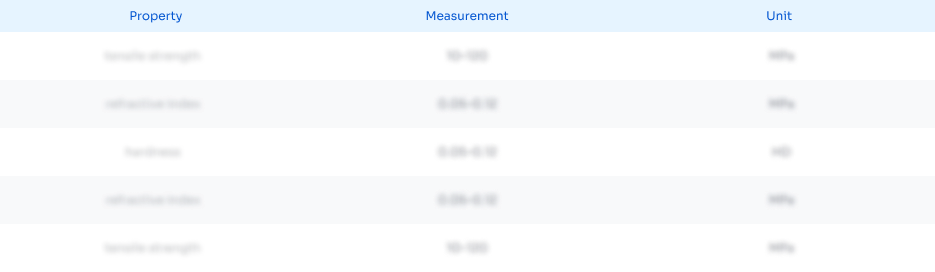
Abstract
Description
Claims
Application Information

- R&D Engineer
- R&D Manager
- IP Professional
- Industry Leading Data Capabilities
- Powerful AI technology
- Patent DNA Extraction
Browse by: Latest US Patents, China's latest patents, Technical Efficacy Thesaurus, Application Domain, Technology Topic, Popular Technical Reports.
© 2024 PatSnap. All rights reserved.Legal|Privacy policy|Modern Slavery Act Transparency Statement|Sitemap|About US| Contact US: help@patsnap.com