Meglumine production process capable of recycling solvent
A production process, the technology of meglumine, which is applied in the field of solvent reuse meglumine production process, can solve the problems of poor dehydration effect, achieve the effects of increased recovery rate, reduced water content, and reduced recovery cost
- Summary
- Abstract
- Description
- Claims
- Application Information
AI Technical Summary
Problems solved by technology
Method used
Examples
Embodiment 1
[0037] The preparation steps of the catalyst are as follows: melt 50g of aluminum at 800°C, melt 7g of rhodium, 40g of nickel, and 3g of chromium at a temperature of 2500°C, then add the molten rhodium, nickel, and chromium to the molten aluminum, stir evenly, and cool , and then the alloy is melted, sprayed, and rapidly cooled by a spray method to obtain an aluminum-nickel-chromium-rhodium alloy, and the particle size of the screened aluminum-nickel-chromium-rhodium alloy is 80-100 mesh.
[0038] Then stir the 25wt% sodium hydroxide solution and raise the temperature to 43°C, then gradually add the aluminum-nickel-chromium-rhodium alloy powder. After 2.6 hours, let cool to 60° C., stop stirring, wash repeatedly with water until the pH is 7, and then wash with absolute ethanol until the content of ethanol in the feed liquid is 96%.
[0039] A kind of meglumine production technique of solvent recycling, comprises the following steps:
[0040] S1: Pass monomethylamine gas into ...
Embodiment 2
[0049] The difference with embodiment 1 is:
[0050]Add sulfuric acid to the mother liquor obtained in step S2 to adjust the pH to 7, add silica gel particles, the mass ratio of silica gel to mother liquor is 1:2.2, and continue to stir and mix for 10 minutes, then filter out the silica gel particles to obtain the filtrate, and add oxidation Calcium and keep stirring, until the calcium oxide no longer reacts, continue to add calcium oxide, and the mass ratio of the calcium oxide to the concentrated sulfuric acid that continues to be added is 1:2, after the calcium oxide is added, add 98wt% concentrated sulfuric acid, until The pH is 7, and the ethanol recovery liquid is obtained by distillation.
[0051] After the silica gel particles filtered out of the mother liquor are dried at 105°C for 1.5 hours, the mother liquor can be further dried.
Embodiment 3
[0053] The difference with embodiment 1 is:
[0054] Add sulfuric acid to the mother liquor obtained in step S2 to adjust the pH to 7, add silica gel particles, the mass ratio of silica gel to mother liquor is 1:2, and continue to stir and mix for 20 minutes, then filter out the silica gel particles to obtain the filtrate, add oxidation Calcium and keep stirring, until the calcium oxide no longer reacts, continue to add calcium oxide, and the mass ratio of the calcium oxide to the concentrated sulfuric acid that continues to add is 1:1.85, after the calcium oxide is added, add the concentrated sulfuric acid of 98wt%, until The pH is 7, and the ethanol recovery liquid is obtained by distillation.
[0055] After the silica gel particles filtered out of the mother liquor are dried at 100°C for 2 hours, the mother liquor can be further dried.
PUM
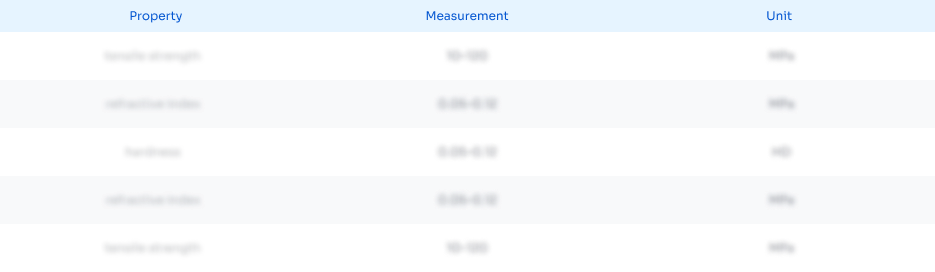
Abstract
Description
Claims
Application Information

- R&D Engineer
- R&D Manager
- IP Professional
- Industry Leading Data Capabilities
- Powerful AI technology
- Patent DNA Extraction
Browse by: Latest US Patents, China's latest patents, Technical Efficacy Thesaurus, Application Domain, Technology Topic, Popular Technical Reports.
© 2024 PatSnap. All rights reserved.Legal|Privacy policy|Modern Slavery Act Transparency Statement|Sitemap|About US| Contact US: help@patsnap.com