A kind of organosilicon modified unsaturated higher fatty alcohol ester defoamer and preparation method thereof
A technology of alcohol ester defoamer and high-grade fatty alcohol, which is applied in chemical instruments and methods, separation methods, foam dispersion/prevention, etc., and can solve the problems of ineffective defoaming of floating foam and surface foam, and poor water filtration of paper machines , poor water dispersibility and other problems, to avoid the problem of paper machine sticking rolls, fast defoaming speed, and strong foam suppression ability
- Summary
- Abstract
- Description
- Claims
- Application Information
AI Technical Summary
Problems solved by technology
Method used
Image
Examples
Embodiment 1
[0041]1) Put octadecylenediol with a molar ratio of 1:0.8 and hydrogen-containing silicone oil with a hydrogen content of 0.05% in the reactor, start stirring and raise the temperature, set the pressure at -0.07MPa, and the temperature at 70°C. The time is 50min, carry out water removal, remove low-boiling impurity treatment, then turn off vacuum, add the 0.1% chloroplatinic acid catalyst of system material gross mass, in N 2 Under a protected environment, the temperature was raised to 95° C. and kept for 4 hours to terminate the reaction to obtain an intermediate.
[0042] 2) Put the intermediate and lauric acid with a molar ratio of 1:2.2 in another reactor and start stirring, start to heat up to 75°C, add 0.5% p-toluenesulfonic acid, turn on the vacuum to -0.08MPa, and start to heat up , the temperature was raised to 130° C. for 8 hours, then the vacuum was turned off, the temperature was lowered and the material was discharged to obtain the product.
[0043] 3) Take 10g o...
Embodiment 2
[0046] 1) Put dodecenol with a molar ratio of 1:1 and hydrogen-containing silicone oil with a hydrogen content of 0.1% in the reaction kettle, start stirring and heat up, set the pressure at -0.08MPa, the temperature at 80°C, and the time Be 30min, carry out dewatering, remove low-boiling impurity treatment, then turn off vacuum, add the 0.2% chloroplatinic acid catalyst of system material gross mass, in N 2 Under a protected environment, the temperature was raised to 105° C. and kept for 3 hours to terminate the reaction to obtain an intermediate.
[0047] 2) Put the intermediate and stearic acid with a molar ratio of 1:1.5 in another reactor and start stirring, start to heat up to 80°C, add 0.3% sulfamic acid, turn on the vacuum to -0.085MPa, and start to heat up , the temperature was raised to 140° C. for 6 hours, then the vacuum was turned off, the temperature was lowered and the material was discharged to obtain the product.
[0048] 3) Take 15g of silicone-modified unsa...
Embodiment 3
[0051] 1) Put octadecenol with a molar ratio of 1:2.5 and hydrogen-containing silicone oil with a hydrogen content of 0.15% in the reactor, start stirring and heat up, set the pressure at -0.09MPa and the temperature at 90 ℃, the time is 20min, carry out dehydration, remove the treatment of low-boiling point impurities, then turn off the vacuum, add 0.5% chloroplatinic acid catalyst of the total mass of the system material, in N 2 Under a protected environment, the temperature was raised to 125° C. and kept for 0.5 h to terminate the reaction to obtain an intermediate.
[0052] 2) Put the intermediate and behenic acid with a molar ratio of 1:0.85 in another reactor and start stirring, start to heat up to 95°C, add 0.1% methanesulfonic acid, turn on the vacuum to -0.09MPa, and start to heat up , the temperature was raised to 165° C. for 2 hours, then the vacuum was turned off, the temperature was lowered and the material was discharged to obtain the product.
[0053] 3) Take 2...
PUM
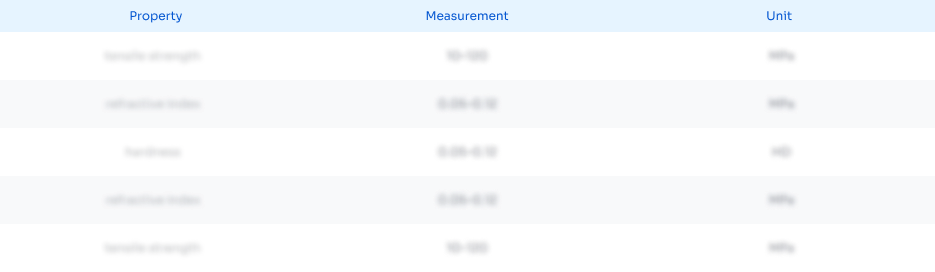
Abstract
Description
Claims
Application Information

- R&D
- Intellectual Property
- Life Sciences
- Materials
- Tech Scout
- Unparalleled Data Quality
- Higher Quality Content
- 60% Fewer Hallucinations
Browse by: Latest US Patents, China's latest patents, Technical Efficacy Thesaurus, Application Domain, Technology Topic, Popular Technical Reports.
© 2025 PatSnap. All rights reserved.Legal|Privacy policy|Modern Slavery Act Transparency Statement|Sitemap|About US| Contact US: help@patsnap.com