Flame-retardant high-temperature-resistant glass fiber reinforced plastic composite material
A composite material and high temperature resistant technology, which is applied in the field of flame retardant and high temperature resistant glass fiber reinforced plastic composite materials, can solve the problems that epoxy glass fiber reinforced plastic is not resistant to high temperature, has no flame retardancy, and cannot be used in chemical and metallurgical fields, and achieves excellent insulation and high temperature. The effect of heat resistance
- Summary
- Abstract
- Description
- Claims
- Application Information
AI Technical Summary
Problems solved by technology
Method used
Image
Examples
Embodiment 1
[0033] A method for preparing a flame-retardant high-temperature-resistant FRP composite material, comprising the following steps:
[0034] Step 1, preparation of self-made flame retardant resin:
[0035] 1) Import 50 parts of aluminum hydroxide into the mixing tank, then spray 1 part of coupling agent on the aluminum hydroxide, and stir evenly while spraying,
[0036] 2) Pour 1.5 parts of antimony trioxide, 1.5 parts of chlorinated paraffin, 10 parts of decabromodiphenyl ether and 40 parts of 191 type unsaturated polyester resin into the mixing tank, and stir in the same direction for 30 minutes.
[0037] 3) Use 1.5 parts of organic phosphorus to adjust the viscosity. If there are many foams, you can drop the defoamer tributyl phosphate for defoaming. Stir for 15 minutes to strengthen the flame retardancy. Take a sample to check the viscosity. , 25°C) to prepare component A,
[0038] 4) Add 60 parts of cyclohexanone peroxide and 1.25 parts of catalyst into component A, stir...
Embodiment 2
[0042] A method for preparing a flame-retardant high-temperature-resistant FRP composite material, comprising the following steps:
[0043] Step 1, preparation of self-made flame retardant resin:
[0044] 1) Import 45 parts of aluminum hydroxide into the mixing tank, then spray 0.5 parts of coupling agent on the aluminum hydroxide, and stir evenly while spraying,
[0045] 2) Pour 2 parts of antimony trioxide, 1 part of chlorinated paraffin, 7 parts of decabromodiphenyl ether and 32 parts of 191 type unsaturated polyester resin into the mixing tank, and stir in the same direction for 20 minutes.
[0046] 3) Use 1 part of organic phosphorus to adjust the viscosity. If there are many foams, you can drop the defoamer tributyl phosphate for defoaming. Stir for 20 minutes to strengthen the flame retardancy. Take a sample to check the viscosity. , 25°C) to prepare component A,
[0047] 4) Add 45 parts of peroxycyclohexanone and 0.9 parts of catalyst into component A, stir well to p...
Embodiment 3
[0051] A method for preparing a flame-retardant high-temperature-resistant FRP composite material, comprising the following steps:
[0052] Step 1, preparation of self-made flame retardant resin:
[0053] 1) Import 55 parts of aluminum hydroxide into the mixing tank, then spray 2 parts of coupling agent on the aluminum hydroxide, stir evenly while spraying,
[0054] 2) Pour 1 part of antimony trioxide, 2 parts of chlorinated paraffin, 15 parts of decabromodiphenyl ether and 45 parts of 191 type unsaturated polyester resin into the mixing tank, and stir in the same direction for 30 minutes.
[0055] 3) Use 2 parts of organic phosphorus to adjust the viscosity. If there are many foams, you can drop the defoamer tributyl phosphate for defoaming. Stir for 20 minutes to strengthen the flame retardancy. Take a sample to check the viscosity. , 25°C) to prepare component A,
[0056] 4) Add 100 parts of cyclohexanone peroxide and 1.5 parts of catalyst into component A, stir well
[...
PUM
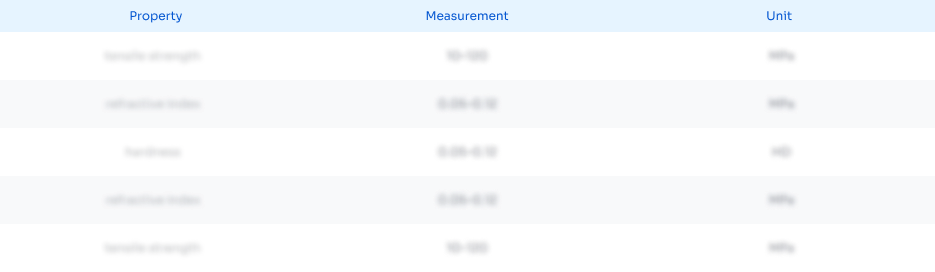
Abstract
Description
Claims
Application Information

- R&D Engineer
- R&D Manager
- IP Professional
- Industry Leading Data Capabilities
- Powerful AI technology
- Patent DNA Extraction
Browse by: Latest US Patents, China's latest patents, Technical Efficacy Thesaurus, Application Domain, Technology Topic, Popular Technical Reports.
© 2024 PatSnap. All rights reserved.Legal|Privacy policy|Modern Slavery Act Transparency Statement|Sitemap|About US| Contact US: help@patsnap.com