Functional composite non-woven fabric preparation method and feeding method and device
A feeding device and material feeding technology, which is applied to the device for coating liquid on the surface, thin material processing, transportation and packaging, etc., can solve the problems of the inflatable shaft, such as heavy weight, aggravating the difficulty of operation for workers, and poor operation convenience
- Summary
- Abstract
- Description
- Claims
- Application Information
AI Technical Summary
Problems solved by technology
Method used
Image
Examples
Embodiment 1
[0102] like figure 1 , 2 As shown, the present embodiment discloses an inclined fastening feeding device, which includes a flipping feeding platform, a lifting platform 12, and a mating fastening device 13. The top of the flipping loading platform is a placement surface 1111 , facing the lifting platform 12 and turning the flipping loading platform upwards can cause the lifting platform 12 to move downward, and the cloth roll on the placement surface 1111 can fall to the top of the lifting platform 12 . Turning back to the lifting platform 12 and turning the flipping feeding platform downwards can cause the lifting platform 12 to move upwards to the cloth roll on the top of the lifting platform 12 and the fastening device 13 is opposite, and the turning of the feeding platform is preferably turned to its placement surface 1111 The height of the end away from the lifting platform 12 is lower than the height of the end close to the lifting platform 12 .
[0103] Two sets of ma...
Embodiment 2
[0150] like Figure 22 As shown, this embodiment discloses a feeding and conveying device based on the inclined fastening feeding device, which also includes a feeding and conveying platform, and the inclined and fastening feeding device and the feeding and conveying platform are arranged according to the process flow from the previous to the last sequence setting. The feeding and conveying platform is provided with a feeding and conveying rotating shaft 211 and a fixed-width lower pressing roller 212. The fixed-width lower pressing roller 212 is fixedly sleeved on the feeding and conveying rotating shaft 211, and two sets of fixed-width lower pressing rollers 212 are respectively distributed on the feeding On both sides of the conveying shaft 211, the feeding and conveying shaft 211 is in rotation with the feeding and conveying platform. A plurality of feeding and conveying shafts 211 are arranged at intervals from front to back and linked with each other through the first fe...
Embodiment 3
[0159] This implementation discloses a method for preparing a functional composite non-woven fabric based on the above-mentioned inclined fastening feeding device, including the following steps:
[0160] Step 1. Feed the PP non-woven fabric roll through the feeding device;
[0161] Step 2, the PP non-woven fabric roll is transported to the coating device for coating; wherein, the coating solution includes the following raw materials in mass fractions: 1-2 parts of chitosan, 1-2 parts of glacial acetic acid, 0.1-2 parts of nitric acid Silver, 5-20 parts of gelatin, 90-100 parts of water;
[0162] Step 3, drying the coated PP non-woven fabric;
[0163] Step 4, the dried PP non-woven fabric is rolled up.
[0164] Preferably, the preparation of coating liquid in step 2 comprises the following steps:
[0165] (1) Chitosan, glacial acetic acid, and water are stirred and mixed for 2 to 3 hours at 60 to 80° C. according to a mass ratio of 1:1:47, to prepare chitosan-glacial acetic ...
PUM
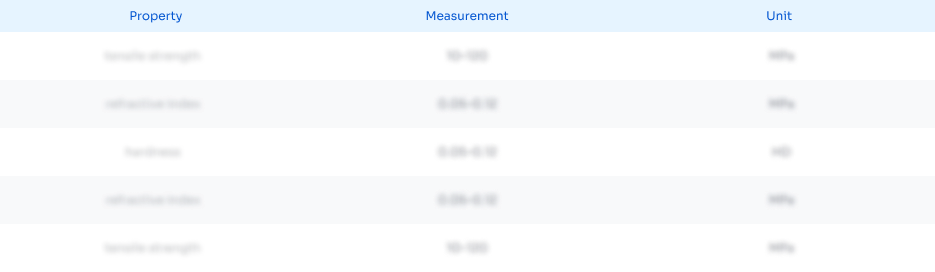
Abstract
Description
Claims
Application Information

- R&D Engineer
- R&D Manager
- IP Professional
- Industry Leading Data Capabilities
- Powerful AI technology
- Patent DNA Extraction
Browse by: Latest US Patents, China's latest patents, Technical Efficacy Thesaurus, Application Domain, Technology Topic, Popular Technical Reports.
© 2024 PatSnap. All rights reserved.Legal|Privacy policy|Modern Slavery Act Transparency Statement|Sitemap|About US| Contact US: help@patsnap.com